As a manufacturer of high-performance granulators for grinding production residues and waste, GETECHA is an established name in plastics and recycling technology. However, the company now also equips its customers with system solutions that cover other stages in the life cycle of polymer products. An illustrative example of this is the realization of packaging and capping systems for blow-moulded bottles and canisters.
A guiding principle in the implementation of closed-loop systems in plastics technology is product lifecycle management (PLM) that is as seamless as possible. This also applies to containers that are manufactured using extrusion blow molding. GETECHA, a company known for its hopper and infeed granulators, has therefore expanded its range to include systems that cover further stages in the life cycle of these hollow body products with the automated capping and packaging of blow-molded bottles, canisters and tanks. “With this expansion of our range, we are continuing on our path to becoming a full-service provider of automated system solutions for plastics processors,” says Christine Rosenberger, Managing Director of GETECHA. In concrete terms, this means that the company no longer only equips users of blow molding technology with granulators for feeding and grinding small and large plastic containers and squeezing slugs, but now also with semi- and fully automatic systems for closing, charging, stacking and film sealing the finished products.

From the pipette to the drum
The models in the company’s RotoCutter series are among the GETECHA granulators that are particularly popular with users of blow molding processes. Where, for example, small pipettes, reject bottles and slugs with volumes of up to 250 ml need to be ground inline or offline, the compact GRS 180/ 300 granulators are often used. They have open three- or four-knife rotors and pick up the material to be ground very well. “For clean room applications, we also supply these granulators with an airlock feed,” emphasizes Christine Rosenberger.
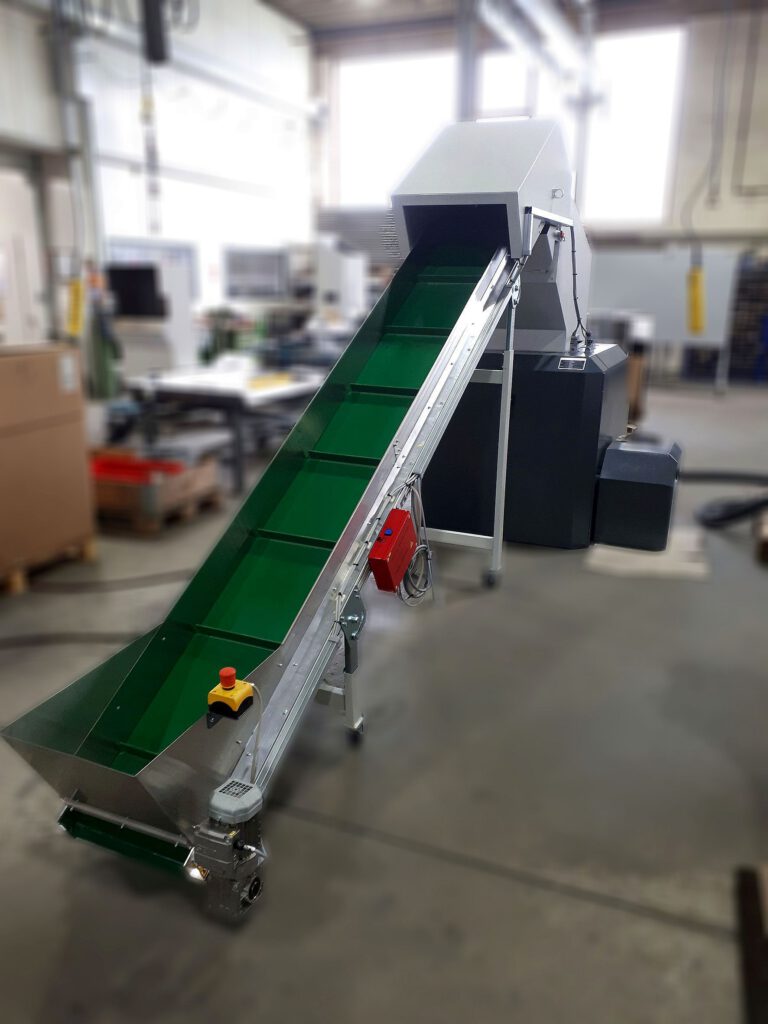
If, on the other hand, canisters and tanks with volumes of up to 30 l are to be processed, many blow molding technicians opt for GETECHA hopper granulators from the RS 2400, RS 30000 or RS 38000 series. They are designed for high efficiency and reliably draw in even large containers despite their small rotor diameters. They are equipped at the factory with super-tangential grinding housings and segment rotors with staggered rows of blades for the rapid intake and shredding of voluminous parts. While an RS 2404-B with 3×2 knives, a rotor cutting circle of 240 mm and a 5.5 kW drive achieves an hourly throughput of up to 160 kg, an RS 38060-B shreds up to 600 kg of material per hour. It also works with 3×2 knives, but has a cutting circle of 380 mm and a 22 kW drive.
Where the volume of rejects or residues is particularly high in blow molding technology, it is the large granulators of the GETECHA RS 8000 series that cover the shredding process step with a cutting circle of 800 mm. They shred tanks and drums with a volume of up to 220 l in a high-quality and energy-saving manner with throughput rates of up to 3,000 kg per hour. “Depending on the industry and environment, we also design these central granulators as clean room models, in stainless steel or as wet granulators – for use in pharmaceutical and food production, for example. Apart from this, almost every one of our granulators is configured to customer specifications and adapted to the specific application with accessory components,” reports Christine Rosenberger
Screw bottles tightly shut
GETECHA has been setting the same standards in terms of customer-specific adaptation for many years in the project planning of infeed and discharge technology as well as exhaust air and big bag systems. However, the company has now also added capping and packaging systems for blow molding technology to its portfolio, specifically with a view to the requirements of plastic container manufacturers. For users who need to close containers, for example, GETECHA produces customized automatic cap-screwing machines. On the other hand, the company equips those whose services include the packaging of finished bottles and canisters with charging and film sealing lines. “In this way, we are now providing our customers with system solutions for further stages in the production of hollow body products. At the same time, we are supporting the implementation of modern closed-loop systems in plastics technology that follow the idea of product lifecycle management,” says Christine Rosenberger.
The cap screwing stations from GETECHA are designed to be so flexible that they are suitable for the application of empty canisters – for dust protection reasons, for example – or for the torque-accurate and tight sealing of filled canisters. Including feed technology, they require a footprint of just 2,000 x 3,500 mm and are suitable for canisters with varying heights (300 – 600 mm) and widths (150 – 300 mm). Depending on requirements, GETECHA produces them in a fully automated version or for manual operation as well as with automatic or manual recipe preselection. With a cycle time of around 13 seconds per cap, such a machine closes up to 330 containers per hour.
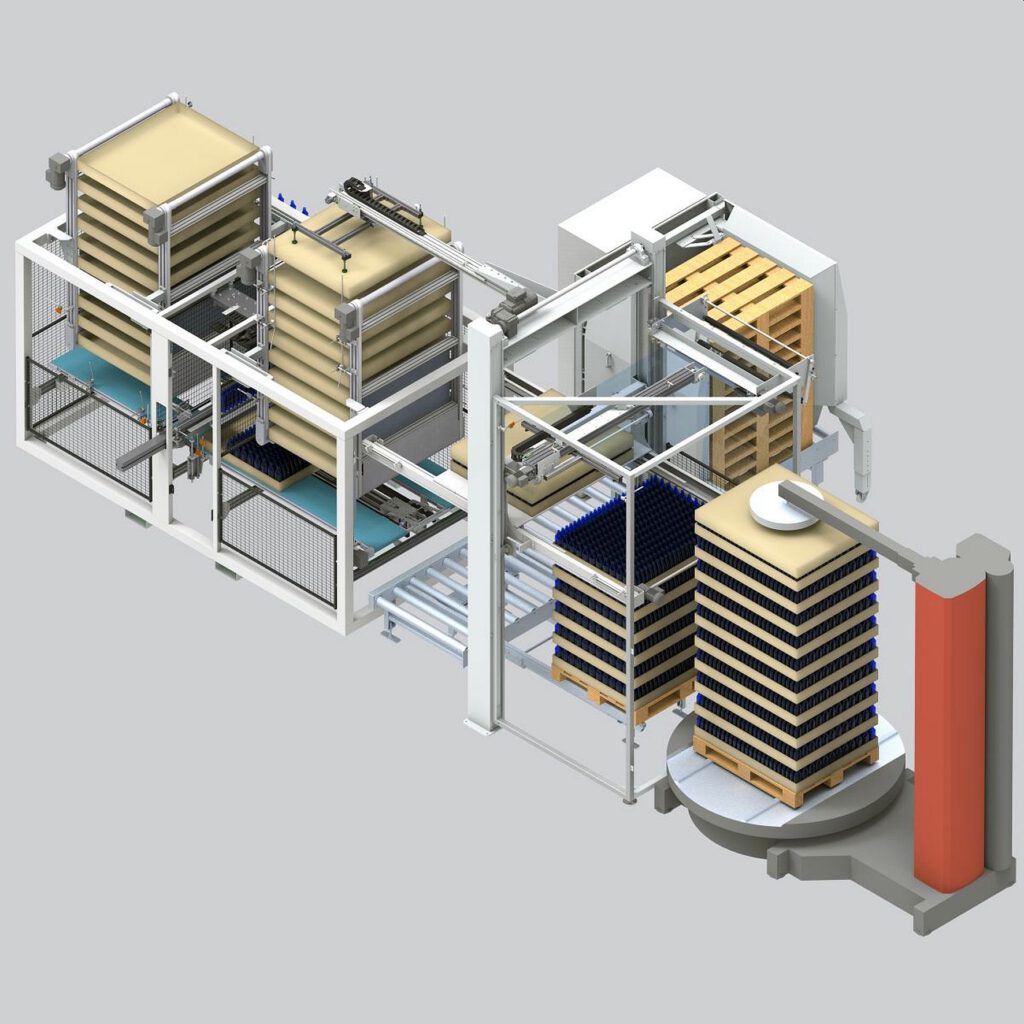
Palletizing, shrink-wrapping and packaging containers
For the charging and packaging of blow-molded bottles, the systems can be provided with varying degrees of automation. In the simplest case as a storage table for manual packaging of small batch sizes or as a semi-automatic or fully automated system solution. As standard, GETECHA designs these lines for round, square and oval bottles with volumes of 100 ml to 2.0 l and for hourly outputs of up to 6,000 bottles. Fully automated, a line of this type includes moving and charging the bottles in rows, separating and presenting the pallets, feeding the trays, folding and gluing the trays, applying layered or stacked film (and lids) and stretch-wrapping and labeling the stacks. “Such a system enables the realization of individual packing patterns and can be integrated into the user’s PDA system. On request, we can also integrate the downstream conveyor technology – for example for material buffering,” says Christine Rosenberger.
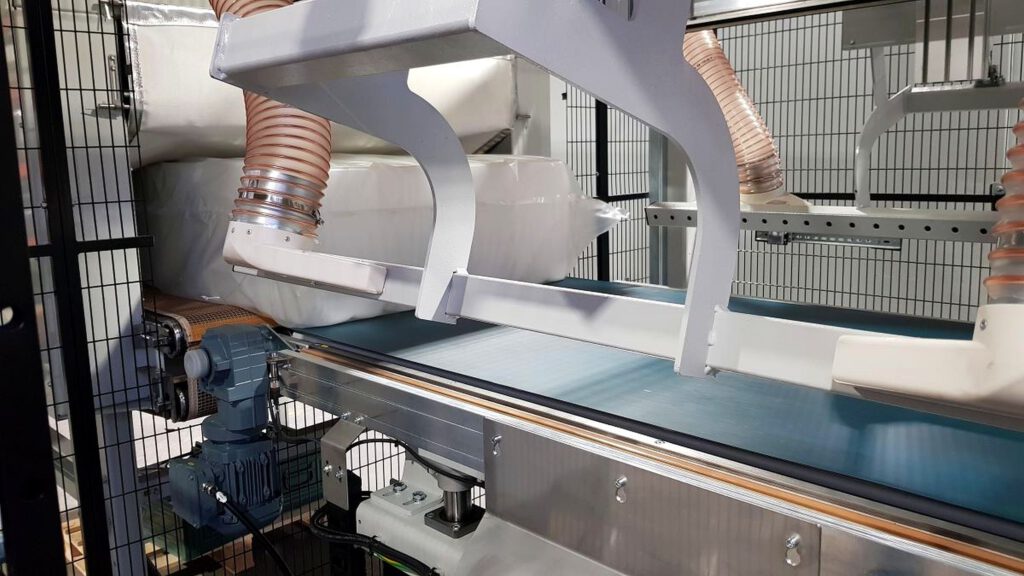
The GETECHA film systems for shrink-wrapping hollow containers are very similar. Even in the standard version, they offer a high degree of efficiency and flexibility, are suitable for canisters with volumes of up to 50 liters and can handle up to 1,200 canisters per hour. All the necessary process steps (stacking, labeling, etc.) are also fully automated, and it is possible to program the canister orientation and adhere to special packing patterns. The output of several blow molding machines with different packaging patterns and container sizes can be combined on such a batching and shrink tunnel system. “In addition, we can integrate the technology of our automatic screwing machines so that the integrated application of caps and the angle- and torque-controlled screwing on of closures is possible,” adds Christine Rosenberger.
As is already familiar from the GETECHA grinding lines, the Aschaffenburg-based company also covers the entire range of services for sealing and packaging systems for blow molding technology, from development to commissioning at the customer’s premises.