The Hansgrohe Group is not only a leading manufacturer of premium products for bathrooms and kitchens, but also a pioneer in the technological implementation of sustainability principles. A current example of this is the commissioning of a fully automated recycling line for processing metallized waste parts from injection moulding production at the Offenburg plant. It was developed in close cooperation with the high-voltage experts from ImpulsTec and the granulator manufacturer GETECHA. Thanks to the innovative system, an almost closed-loop raw material cycle can currently be realized.
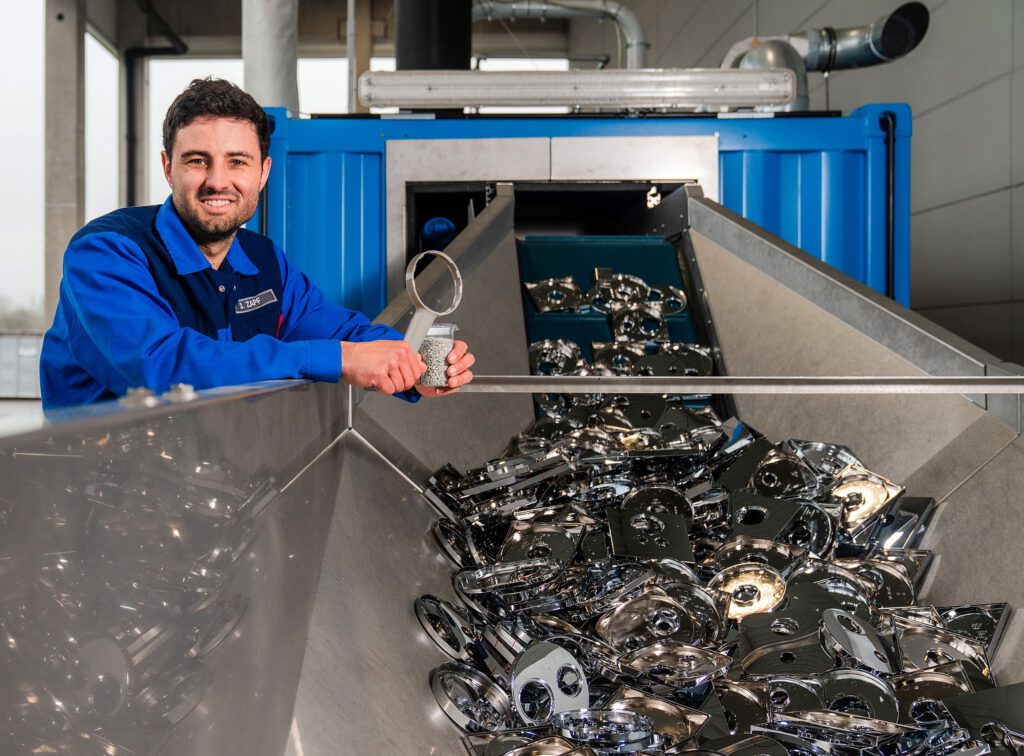
Those responsible at Hansgrohe have been relying on grinding technology from GETECHA for some time now. Last year, when project manager David Zapf, in his role as Specialist Surface Technology at Hansgrohe, was tasked with laying the foundations for the development of a new recycling plant for the reprocessing of chromated faulty parts from injection molding production, system solutions from the German granulator manufacturer were once again used. This time it was an energy-efficient RS 30060 granulator and a GA 500 suction system that proved to be the ideal solution for the new recovery line after various test runs. They cover the process steps of pre-grinding and regrind cleaning (including exhaust air filtration). Their performance is crucial for the quality level that can be achieved during the subsequent decoating of the injection-molded parts and the separation of the raw materials into a proportion of plastic – in this case ABS – and a proportion of metal – in this case a mix of nickel, copper and chrome.
For the realization of the new recycling plant, David Zapf not only intensified his cooperation with GETECHA, but also brought the high-tech company ImpulsTec on board. Picture: Hansgrohe
Direct recycling of raw materials
The chromating of wet room products (e.g. shower heads) not only enhances their appearance, but also preserves their value, as it protects the surfaces from corrosion and mechanical damage. In most cases, the coating is only around 40 µm thick and can account for up to 15 percent of the product weight. However, at Hansgrohe, only injection-molded parts with absolutely flawless chromating survive the strict quality assurance of electroplating, which is why a constant volume of faulty parts is routinely produced. In view of the positive experience that the company had already gained with its in-house raw material cycles for non-metallized rejects, about two years ago the desire arose to establish such a cycle for the chrome-plated ABS moulded parts as well. According to David Zapf, the clear objective here was “to demetallize the coated products in such a way that the plastic content can be fed back into the company’s own new parts production, while the highly concentrated metallic content can be sold on the market.”
In order to realize this project, the surface expert not only intensified its cooperation with GETECHA, but also brought the high-tech company ImpulsTec on board. The reason: based on high-voltage impulse technology, the Radebeul-based special machine manufacturer has developed a highly regarded process that makes it possible, among other things, to separate metallic thin layers from chrome-plated ABS components by means of electrohydraulic shock wave treatment. An important prerequisite for achieving optimum efficiency in this process is the reliable comminution of the galvanized defective parts into a ground material with a homogeneous grain size and low dust content. “Our plan for the new recycling plant therefore gradually took shape as a highly automated processing line in which the continuously fed defective parts primarily pass through three process steps: Firstly, systematic pre-grinding with dust extraction, then separation of the chrome layer using the shock wave process, and finally magnetic separation, so that we obtain two unmixed plastic and metal fractions that we can feed into granulation on the one hand and marketing on the other,” reports David Zapf.
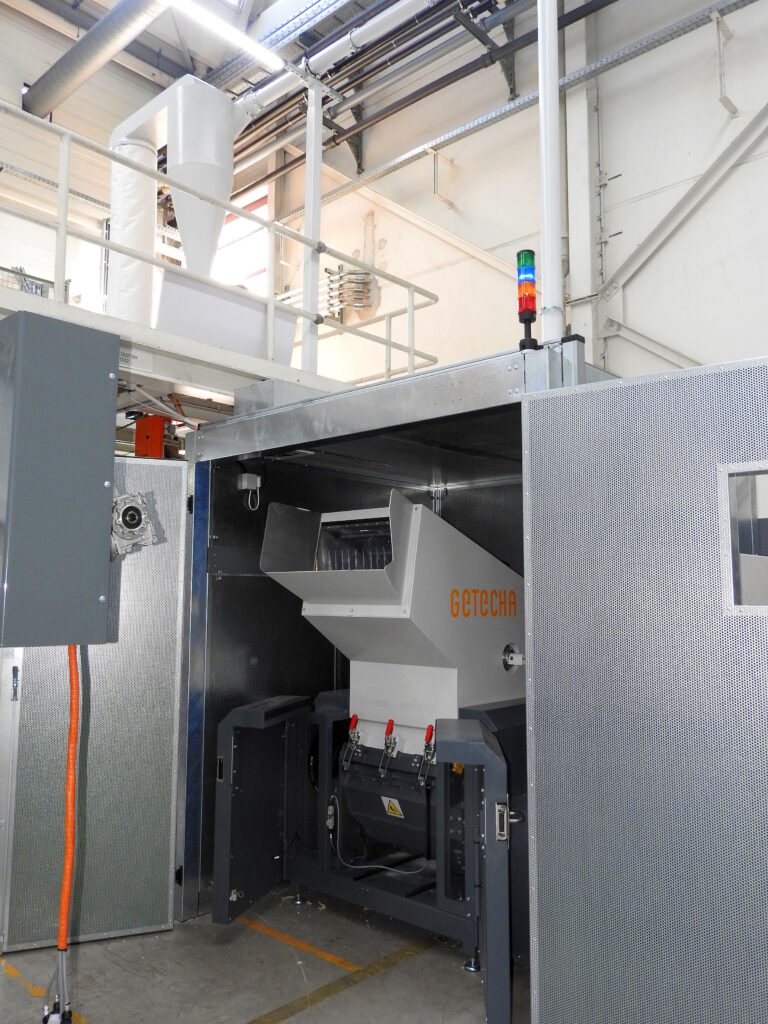
Granulator and suction system from one source
As with previous projects, Hansgrohe’s project manager entrusted GETECHA with key areas of the pre-grinding process. This means that the Aschaffenburg plant manufacturer not only provided the granulator – in this case a Rotary Cutter RS 30060 – but also the dust extraction and exhaust air system for cleaning the ground material. “That proved to be ideal. Because we were able to connect directly to the process technology components of our material-selective electrohydraulic shock wave technology – such as the liquid medium reactor. At the same time, this ensured right from the start that our process can always work with optimally conditioned regrind,” emphasizes Stefan Eisert, Managing Director of ImpulsTec.
The RS 30060 from GETECHA is a modularly designed, compact hopper granulator with a cutting chamber opening measuring 640 x 410 mm and a rotor cutting circle of 300 mm. Based on the scissors-cut principle, 3 x 2 rotary blades and two stationary blades grind the waste parts fed in, which can have diameters of up to 500 mm and wall thicknesses of up to 8.0 mm. The rotor turns at around 420 rpm and is driven by a 15 kW three-phase motor in IE3 design. The special quality features of the granulator include the external rotor bearing, which represents a significant safety advantage, and the geometric precision of the cutting circle, which guarantees a consistently homogeneous grinding result. Other design highlights include the segmented rotor structure, the solid belt pulley – which provides additional flywheel mass – and the overall good accessibility of all important components.
For use in Hansgrohe’s recycling plant, GETECHA equipped its RS 30060 hopper granulator with a cutting housing with integrated sound insulation enclosure and a noise protection cabin. Image: Getecha
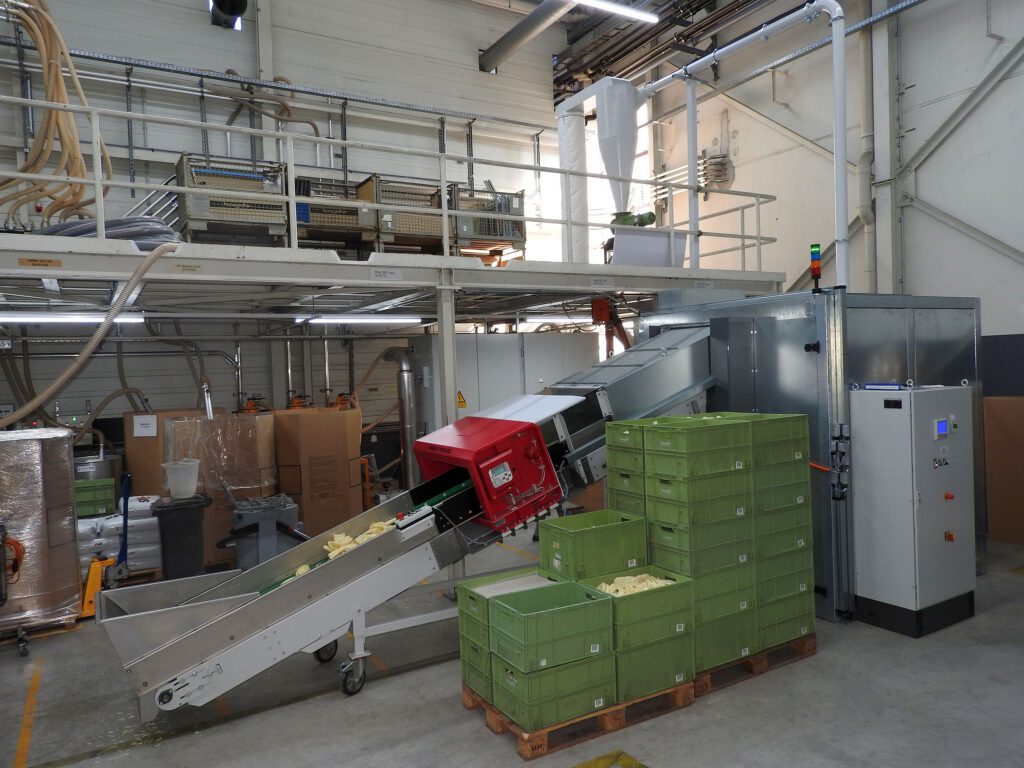
Tailor-made process solution
For use in Hansgrohe’s new recycling plant, GETECHA equipped the granulator with special cutting blades whose cutting geometry is precisely tailored to the grinding requirements of coated plastics. In addition, it was lined around the cutting housing with an integrated sound-insulating enclosure with double-walled insulating material and set up in a noise protection cabin on four rubber mountings. For maintenance and cleaning, the hopper and cutting chamber can be easily opened with a spindle and locked with a quick-release fastener. While the stationary blade can be fitted to the fixed stop in a few simple steps after grinding or replacement, the roatary blades can be easily preset in the gauge supplied so that the cutting gap is always correct. The screen (6 mm round perforation) can be removed without tools. All surfaces are machined and smooth on all sides for easy maintenance. “All of this reduces the maintenance effort for the granulator and ensures its high availability,” emphasizes Andreas Lanz, Area Sales Manager at GETECHA.
Control technology integrated
In terms of control technology, the GETECHA granulator also fits homogeneously into the overall structure of the recycling plant. For example, to ensure continuous material feed and prevent overfilling of the cutting chamber, the conveyor belt used for this purpose is controlled by the load-dependent control system of the granulator with the incoming faulty parts and sprues. In addition, the production and system status of the granulator is continuously monitored and a visual display signals the current operating mode. All processes are automatically recorded in total and transmitted to the system operator via a mobile data network. The granulator has an integrated control cabinet with easy-to-understand controls.
Depending on the material and feed, the RS 30060 from GETECHA is designed for an hourly throughput of up to 400 kg and grinds the chrome-plated ABS molded parts – depending on the perforation of the screen – into a regrind with grain sizes of 5.0 mm, for example. In Hansgrohe’s recycling plant, the regrind is then extracted from the granulator’s screen carriage using the GA 500 S suction system from GETECHA and separated in a cyclone. A rotary valve ensures that the regrind is separated from the air and discharged in a pressure-neutral manner. The integrated filter system – also from GETECHA – cleans the exhaust air and returns it to the environment. In the subsequent process, the plastic is separated from the metallic adhesions using ImpulsTec’s shock wave process and the two material fractions are separated and dried.
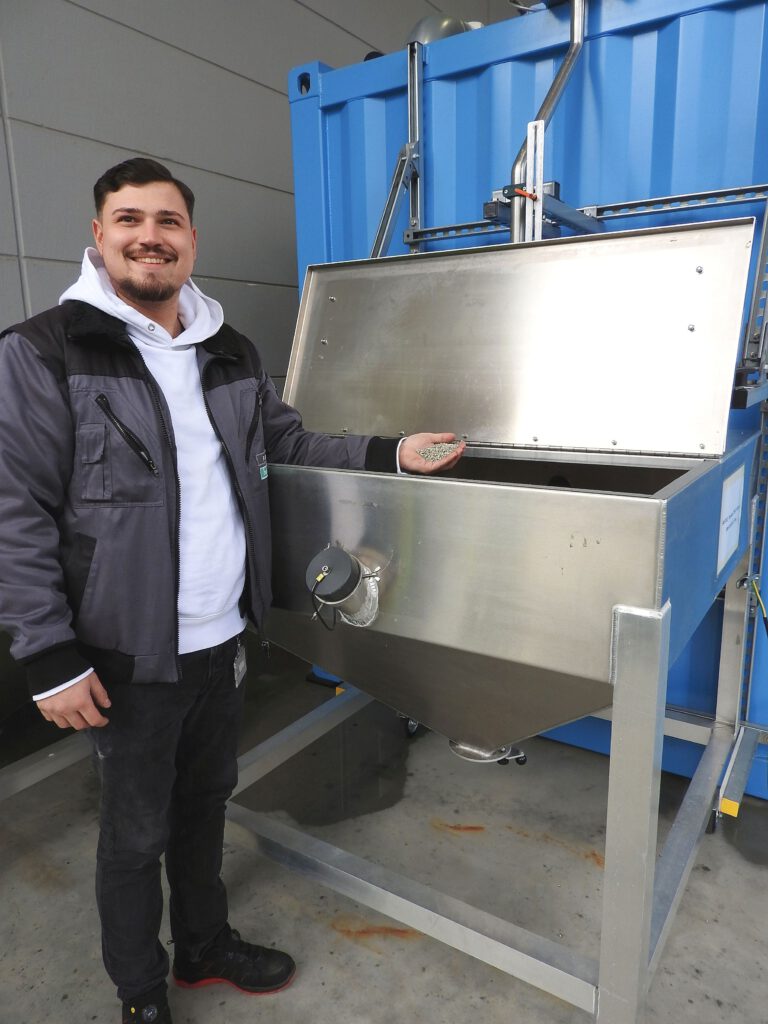
Highly innovative with great potential
When the recycling plant went into operation in mid-2024, it was clear to everyone involved that this was a highly innovative and perhaps even unique system solution. Thanks to the new processing line, Hansgrohe can currently reuse almost 98% of its raw materials. “On the one hand, we obtain a highly concentrated metal fraction, which primarily contains copper and nickel and is sold for smelting. This means that 100 percent of these recyclable materials are returned to the raw material cycle. On the other hand, we receive the decoated ABS, which we use to manufacture new parts. This closes the recycling loop at the site,” says Pascal Dengler, who is responsible for the smooth operation of the recycling plant.
Incidentally, as the new recycling system is designed for the demetallization of up to 100 tonnes of chrome-plated plastic per year, it has now enabled Hansgrohe to produce a hand shower product line for the premium Hansgrohe brand in which recycled granulate is used without exception.
Pascal Dengler: “In addition to a highly concentrated metal fraction, Hansgrohe receives perfectly demetallized ABS from its new recycling plant, which is reused for the production of new parts.” Picture: Hansgrohe
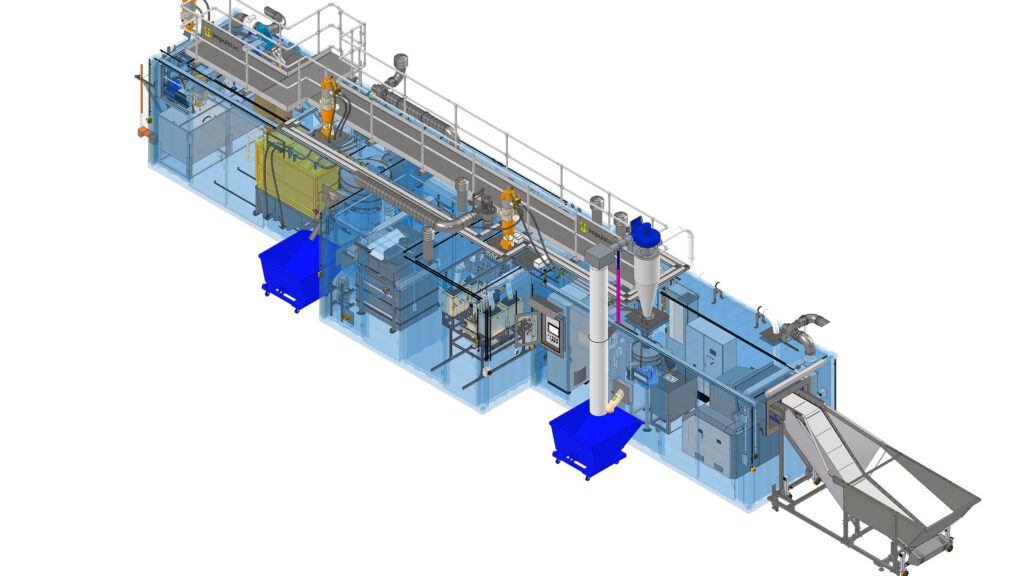
The new recycling plant is an automated processing line in which the galvanized defective parts first pass through a pre-grinding process with dust extraction, followed by a shock wave process and finally magnetic separation. Pictures: Hansgrohe/ ImpulsTec