Getecha granulation technology enables recovery of extrusion waste
Everywhere in the plastics industry, waste and residue from production are fed into treatment circuits, and are recycled as recyclable materials. In order to enable this automated and highly efficient recovery plants, the German company Getecha provides an attractive portfolio of mostly standardised granulators amongst others. Here you can read how a manufacturer of drive belts was able to use this to organise the recycling of plastic granulate from the edge trims of his extrusion lines.
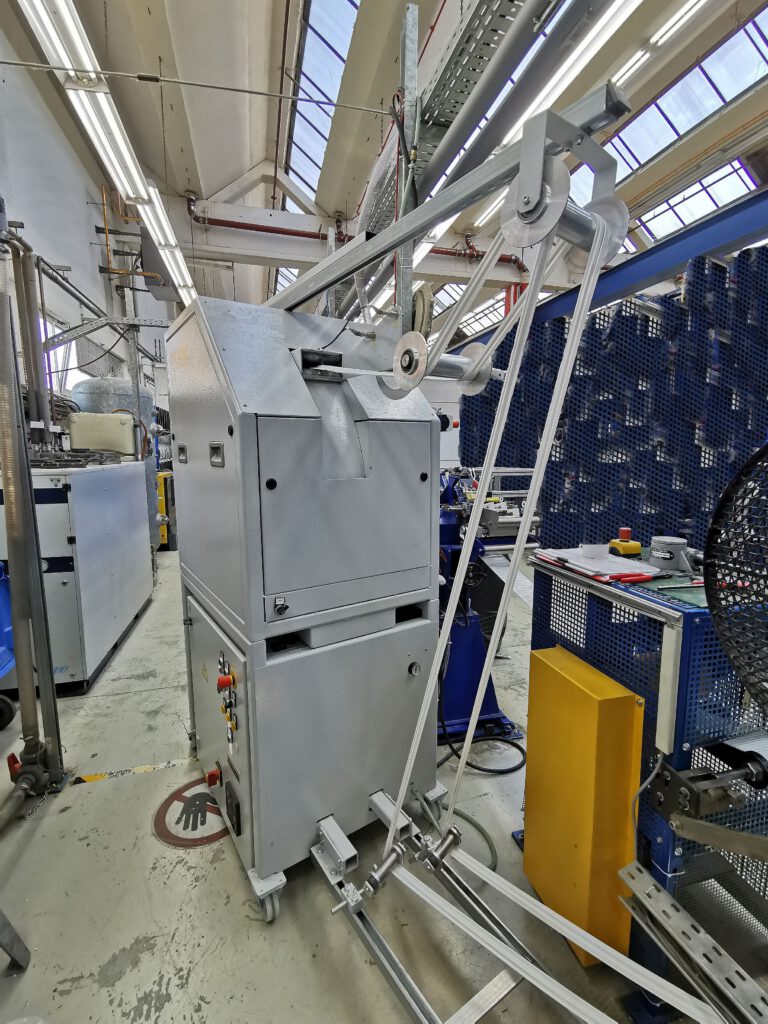
Photo 1: On an extrusion system for th eproduction of drive belts and conveyor belts, the granulator RS 2402-E from Getecha simultaneously pulls in two edge trims made of TPE or TPU 50-95 Shore A and granulates them to rpoduce high-quality ground material.
“Whether it is during extrusion or assembly of foils, foams and panels – the continuous extraction of plastic granulate from edge trims provides plastics processors with an excellent opportunity to reduce their raw material, logistics and disposal costs. Reusing the recycled material had a positive effect on the production volume and yields, and the associated reduction of material loss contributes to the sustainability of the whole company”, says Eva Rosenberger. The expert for recycling technology, Sales Manager and shareholder of the plant construction company Getecha knows what she is talking about. This is because starting with the granulation, handling and extraction systems of the company from Aschaffenburg in Germany, she is repeatedly involved in the implementation of numerous projects for the realisation of modern recovery and recycling solutions in the plastics industry. For example, Getecha recently took on the task from a reputable manufacturer of drive belts and conveyor belts who required granulators.
In parallel to the cycling of the extrusion or assembly systems, they were expected to continuously and simultaneously pull in, granulate and provide two edge trims made of TPE or TPU 50-95 Shore A – occasionally also with integrated inlays made of steel – for further processing. This time, the infeed granulators of type RS 2402 E of the well-known RotoSchneider series from Getecha were chosen. “This machine is part of a highly successful model series, which is perfectly adapted to the production of high-quality ground material, which can be recycled or added to the new material”, says Eva Rosenberger.
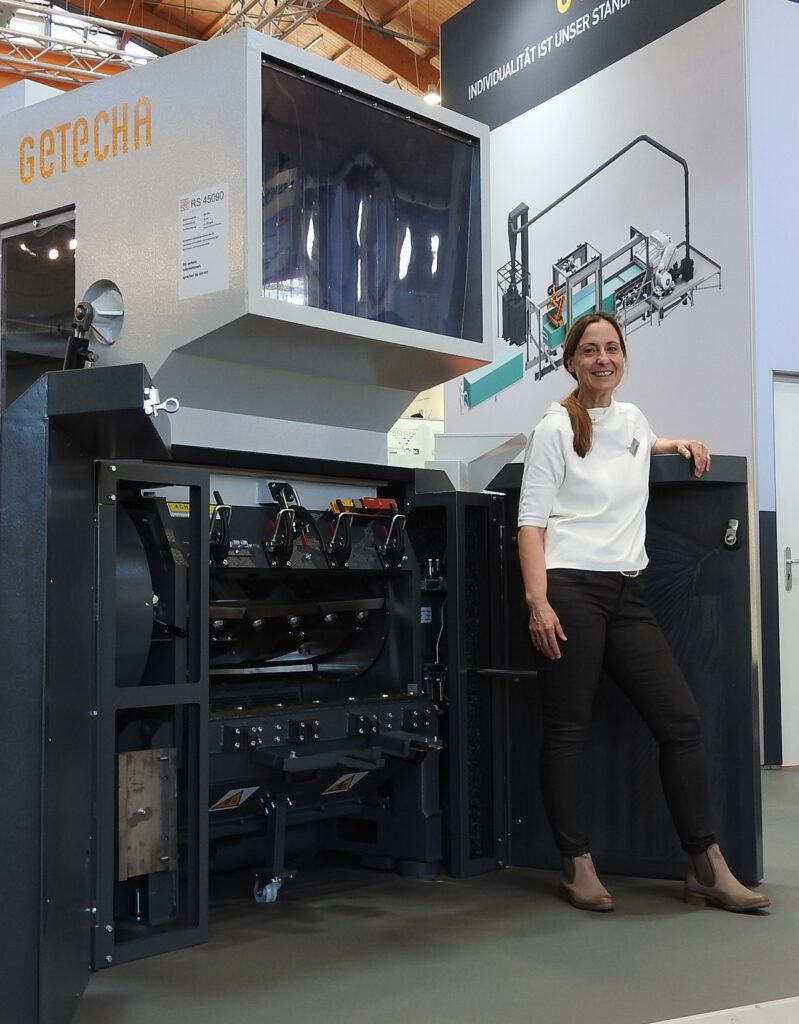
Photo 2: Eva Rosenberger (here in front of a large central granulator of her company)
Compact and customer-specific
As for many other projects of this kind, the system solution from Getecha in this case is also based on the application-specific customisation of a standard system. Adapted to the specific requirements of the drive and conveyor belt manufacturer, the RS 2402-E machines were equipped with 4 kW drives, which provide the infeed granulators with granulation performance of up to 80 kg of ground material per hour during running operation. At the request of the customer, they also received sound-insulated, compact and stable machine frames with integrated switching cabinet, which are made mobile by means of guide rollers.As their design is very slender (750 x 1,970 x 1,810 mm), they can be positioned space-efficiently directly next to the assembly or extrusion lines. And as it was necessary to feed the edge trims to be shred from ground level already, Getecha equipped the granulators with additional arms and pulleys.
Apart from the customer-specific modifications, the RS 2402-E from Getecha is characterised by a multitude of technical intricacies. For example, this includes the roller deflection with a floating roller of a dancer arm type, which ensures a particularly material-friendly pulling off of the edge trims from the trimming systems, and compensates the traction and vibrations affecting the edge trims. While two knurled infeed rollers inside the granulator also counteract the transmission of vibrations onto the edge trims, integrated sensors detect excessive traction and limit the infeed if there is a risk of tearing. Furthermore, a two-part hopper in front of the infeed opening enables simultaneous feeding in of two edge trims into the roller infeed, without them crossing each other and getting tangled. Ultimately, for the production of the drive and conveyor belt manufacturer, all these measures make sure that the edge trim infeed is efficient, practically trouble-free and always adapted to the speed of the extrusion or assembly system.
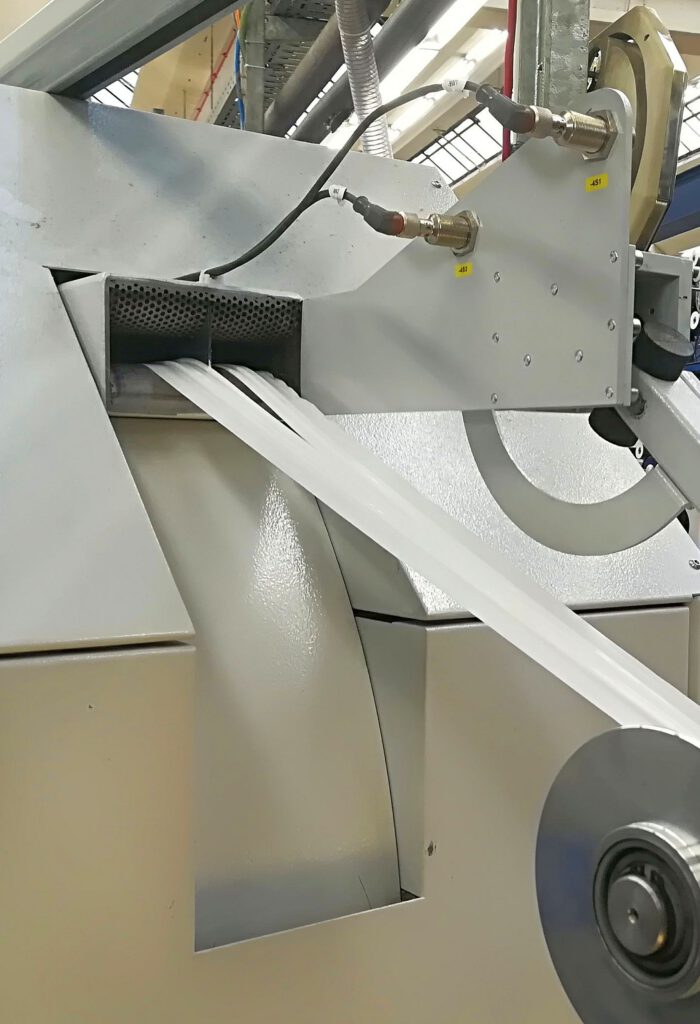
Photo 3: The two-part hopper of the RS 2402 E from Getecha enables the simultaneous feeding in of two edge trims into the roller infeed, without them crossing each other and getting tangled.
From ground material to reusable material
“The correct design of the granulation system and synchronisation of the infeed speed are key factors for its successful integration into the product environment. However, just as important are the requirements of the customer with regard to the quality of the ground material”, says Eva Rosenberger. For this reason, amongst others, the RS 2402 E has an intelligent control for regulating the infeed speeds, which also includes an automatic switch to buffer operation. When the minimum infeed speed is undercut, this control developed by Getecha prevents the generation of obstructive fine material and undesirable dust particles during granulation, thus ensuring that the granulator always produces clean ground material of excellent quality even with low infeed speeds in the range of 0 – 6.0 m/min.
Eva Rosenberger: “This is achieved by automatically switching into buffer mode, while simultaneously undercutting the optimum outfeed speed. The dancer arm is used as material storage here, and the infeed is activated and deactivated depending on the position of the dancer arm, which thus determines the storage volume.”
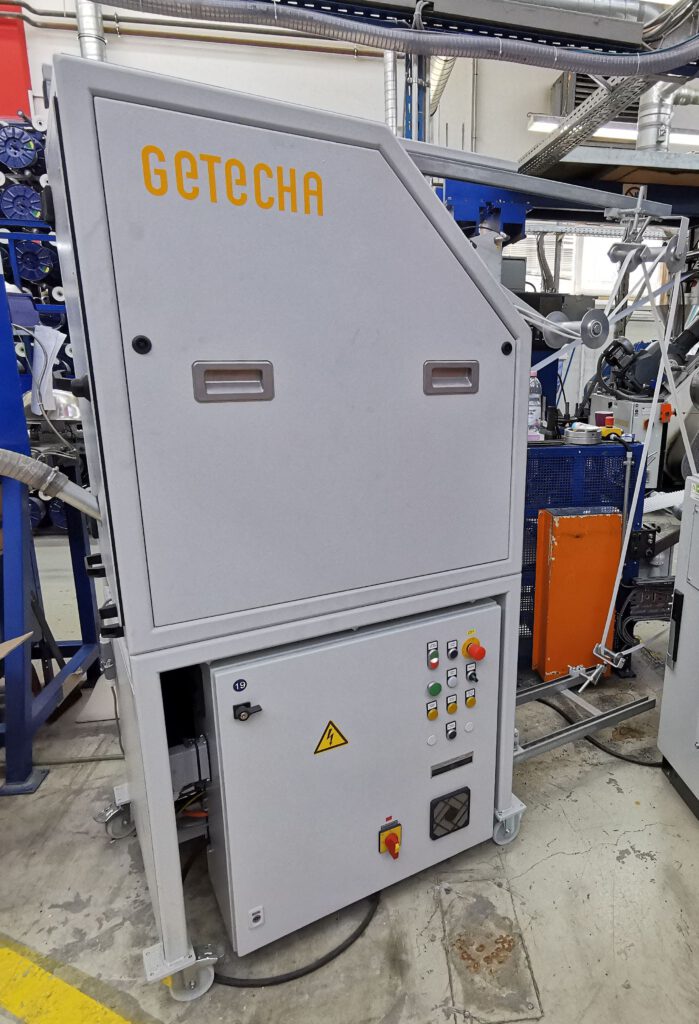
Photo 4: The design of the mobile unit is very slim and space-saving, and can be positioned directly next to the assembly or extrusion line.
Quality from the first cut
In addition to the intelligent control and buffer operation, there are two additional factors with which the RS 2402 E provides the drive and conveyor belt manufacturer with high ground material quality: First of all, optimum ventilation of the ground material during the granulation process, preventing potential material heating, and supporting optimum material flow when processing elastic materials, even at larger quantities. And secondly, the use of a very sturdy and openly designed three-knife-rotor with powerful cutting. It has a diameter of 240 mm, provides a cutting length of 226 mm and is equipped with blades of highly quenched and tempered carbide, which are characterised by excellent cutting capacity and long service life. In case the infeed of third party material such as steel inlays cannot be excluded, blades of normal quality or high-speed steel (HSS) can also be inserted. s the fed in edge trims are directly guided via the double roller infeed of the RS 2402 E between the rotor and stator blade, it is ensured that the best possible ground material geometry is produced with the first cut already. “This is an important technical prerequisite to achieving an excellent granulation performance and outstanding ground material quality”, says Eva Rosenberger.
Sustainability
Through its use, a modern infeed granulator such as the RS 2402 E from Getecha not only contributes to the establishment of sustainable production methods in plastics processing, but is itself a successful example of development and engineering, which is consistently based on the principles of sustainability and energy efficiency. This way, the RotoSchneider rotary cutters from Getecha can be equipped with the innovative EnergySave system of the plant construction company amongst others, which reduces its electrical energy consumption under partial load by up to 40 percent. Eva Rosenberger also refers to more “additional options for energy data acquisition and reduction in consumption, which can be selected individually.” The high quality of the carbide blades from Getecha also contributes to lowering the operating and maintenance costs. The effort alone for replacing and regrinding the blades is thus significantly reduced. If filled plastics are granulated, required intervals for regrinding are significantly extended.
Economical complete solutions
With its broad range of granulators as part of the RotoSchneider line, as well as the guillotine shears of the GH series and the foil cutters of the FS series, Getecha provides extensive options for the realisation of modern system solutions for production-related material recovery at a scale between 10 and 5,000 kg/h. The range of services offered by the plant construction company from Aschaffenburg also always includes the provision and customised design of conveying and suction technology for the feeding of edge trims, as well as collection and forwarding of the ground material. For example, in the case of the drive and conveyor belt manufacturer, it was discussed whether the ground material should be collected below the system following granulation, whether it should be extracted by suction by means of a suction conveyor on customer side, or whether it should be forwarded to the place of further processing via an extraction system from Getecha. “In order to ensure the cost effectiveness and efficiency or our complete solutions, a detailed requirement analysis is carried out for each project in advance, including a projected calculation for the costs and consumption”, Eva Rosenberger explains.