The granulation of sprues and faulty parts in production is the standard for most injection moulders. Parts for medical technology are usually produced in clean rooms. The low particle rates permitted have so far banned granulation in separate rooms.
A manufacturer of parts for inhalers realized the economic advantages of immediate recycling of sprues and faulty parts in his clean rooms.
Installation:
The proven GRS 180 beside-the-press granulator is equipped with the following options for this application:
- The standard hopper is replaced by a hopper with two pneumatic operated flaps. The flaps open and close time delayed. Therefore the cutting chamber is always closed and fly-back material cannot spray to the outside.
- The cutting chamber is additionally sealed.
- The controlling of the flaps is done by a small PLC. The programmed operating methods allow a very flexible use.
Manual: Input of cycle times by the operator.
Automatic: An interface synchronizes the flap movement to the injection moulding machine. The sprues can be fed during each cycle or after a selected number of cycles. - The position of the flaps is monitored by sensors. If a sprue gets caught between the closing flap and the hopper wall, the flap opens and closes again. This virtually eliminates malfunctions.
After the granulator was put into operation, the customer monitored the particle count of the clean room and could not detect any change.
The GRS 180 has proven itself in this special equipment at various injection moulding companies that produce in a controlled area/clean room.
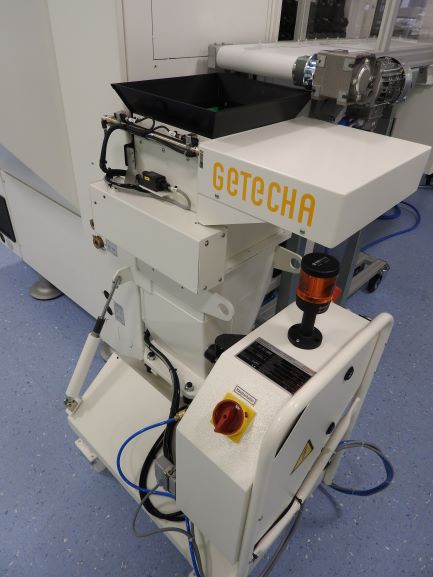