Application
In a blow molding plant the top and tails and the start-up jerry cans are to be ground. Between 10 and 30 l cans are produced on several blow moulding lines.
A granulator is assigned to each blow moulding machine. For the customer the space required on the blow molding machine is decisive. Therefore he planned a separate recycling room. The customer used belt conveyors to transport the top and tails, which he installed at a height of about 3 m. In this way, the space around the blow molding machines was retained solely for the production processes.
Due to the longer transport on the belt conveyors the top and tails could cool down better. The top and tails usually arrived at the granulator in isolated instances. Occasionally, however, they accumulated at the transfer points of the belt comveyors. An operator manually feeds the start-up jerry cans to the granulator.
Installation
The following criteria were decisive in the selection of the granulator:
- reliable granulation of several top and tails at the same time
- quick granulation of the start-up jerry cans
- and fast cleaning of the granulators at colour change
Several RS 3806 were used, which are characterized by the following features:
- cutting diameter 380 mm, cutting width 630 mm, 30 kW
- open 3-blade rotor for optimal grabbing of the jerry cans, segmented rotor with v-cut
- The optimized feed hooper made it possible to use a standard machine. The jerry cans are immediately grabbed by the rotor. There is no jumping and canting.
- Due to the all-side machined surfaces of the cutting chamber and the rotor, the cleaning is done very quickly.
The regrind is sucked out of the granulators and transported to the customer’s silos.
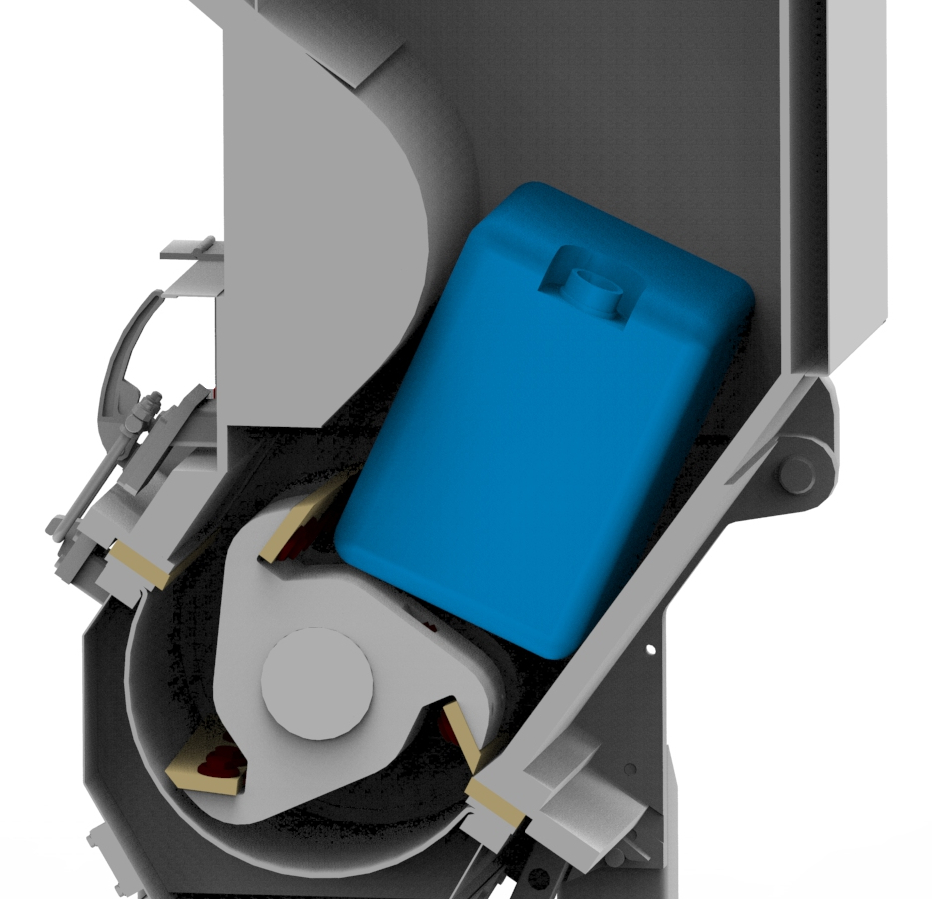
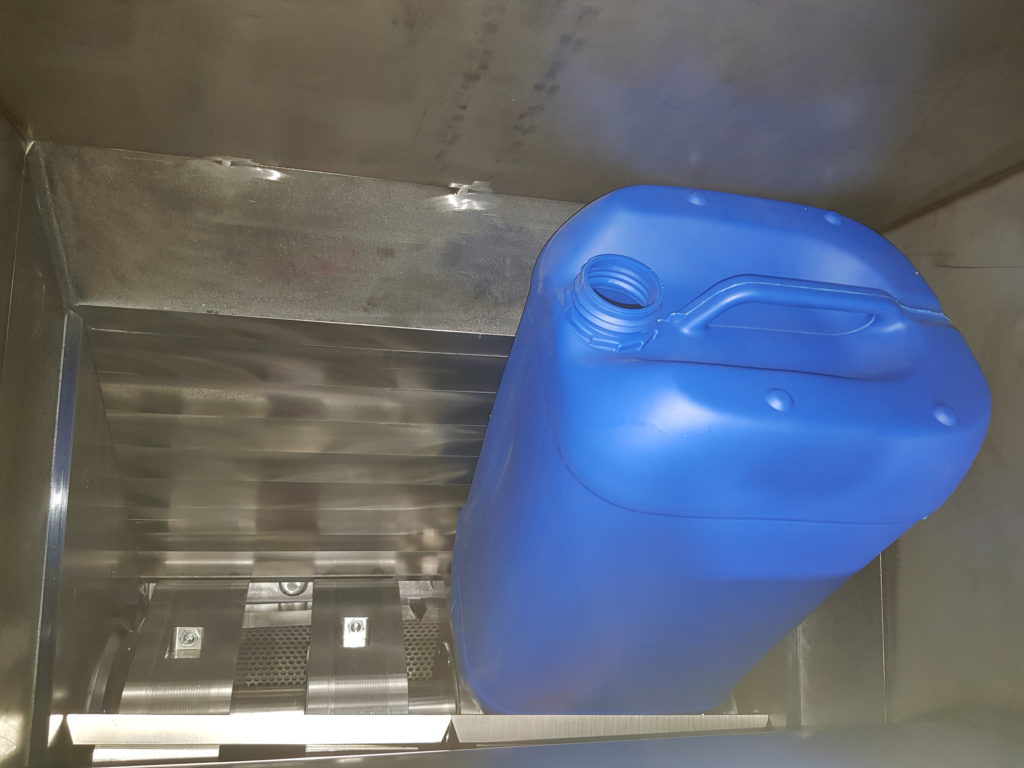