The granulators with wide infeed are installed
- as central granulator for grinding of sheet rolls from an unwinder (off-line)
- direct behind a thermoforming line
- in low built version underneath a punch.
The feed rollers can be smooth (standard), knurled or toothed. With larger roller diameters it is also possible to grind sheet with thermoformed parts.
The infeed speed of the granulator can be controlled by the production line.
For stand alone solutions our automatic speed adjustment makes the work easier for the operator. By evaluating the dancer movement and position, the current average feed speed of the thermoforming machine is determined and forwarded to the infeed of the granulator. The operator can therefore focus fully on the production, manual adjustment of the speed is no longer necessary!

Advantages
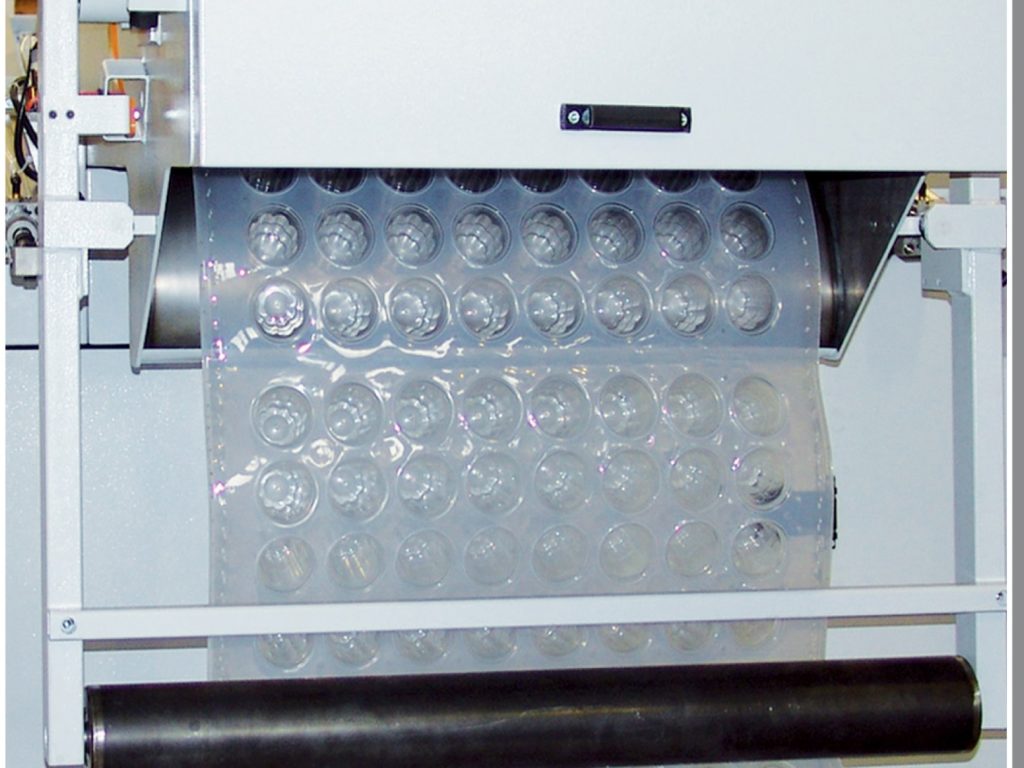
High reliability
- pneumatically adjustable and balanced dancer keeps sheet tight and also avoids excessive tension
- adjustment to line speed by frequency-controlled infeed
- adjustable strippers prevent windings
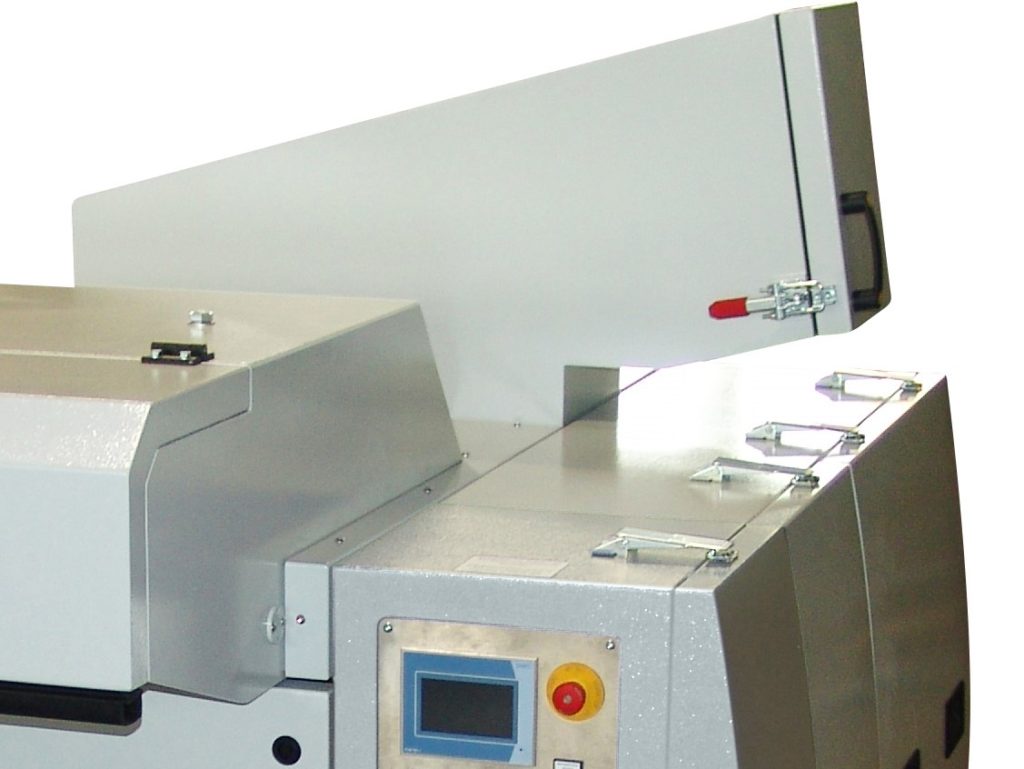
Quiet granulation
- integrated sound insulation
- cutting device is isolated from base frame
- low rotor speed for noise reduction and low dust in the regrind
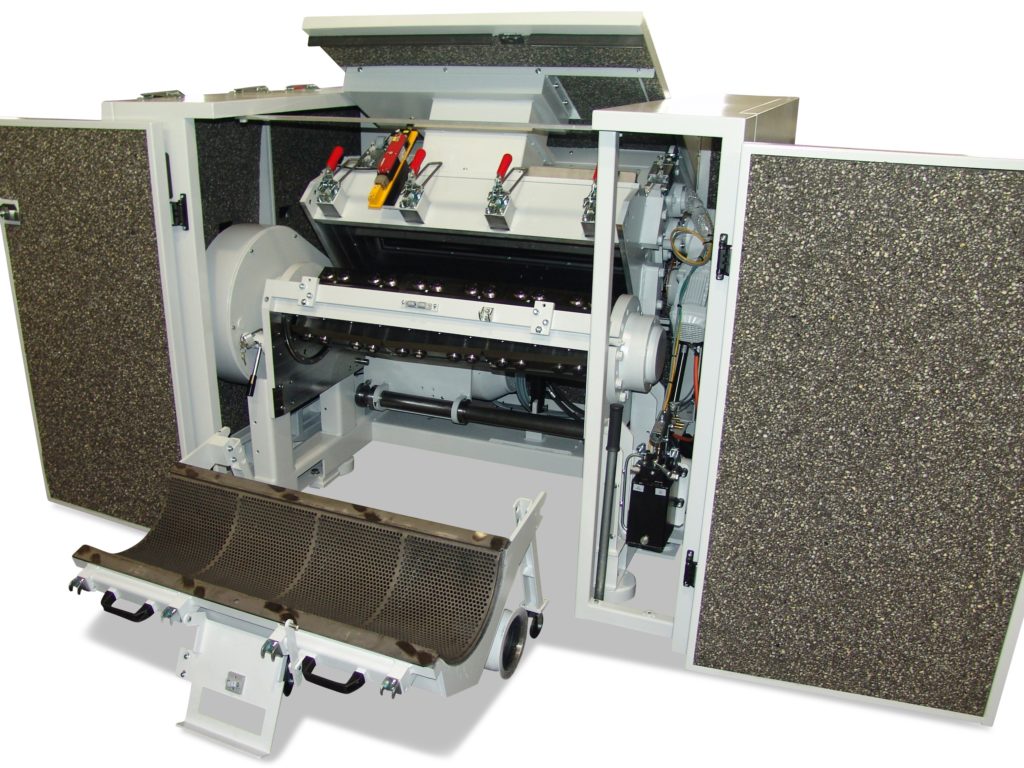
High efficiency
- opening of infeed and cutting chamber without tools
- screen holder removable
- low cleaning time due to smooth, all-side machined surfaces
- high energy efficiency due to cutting geometry and EnergySave motor controller
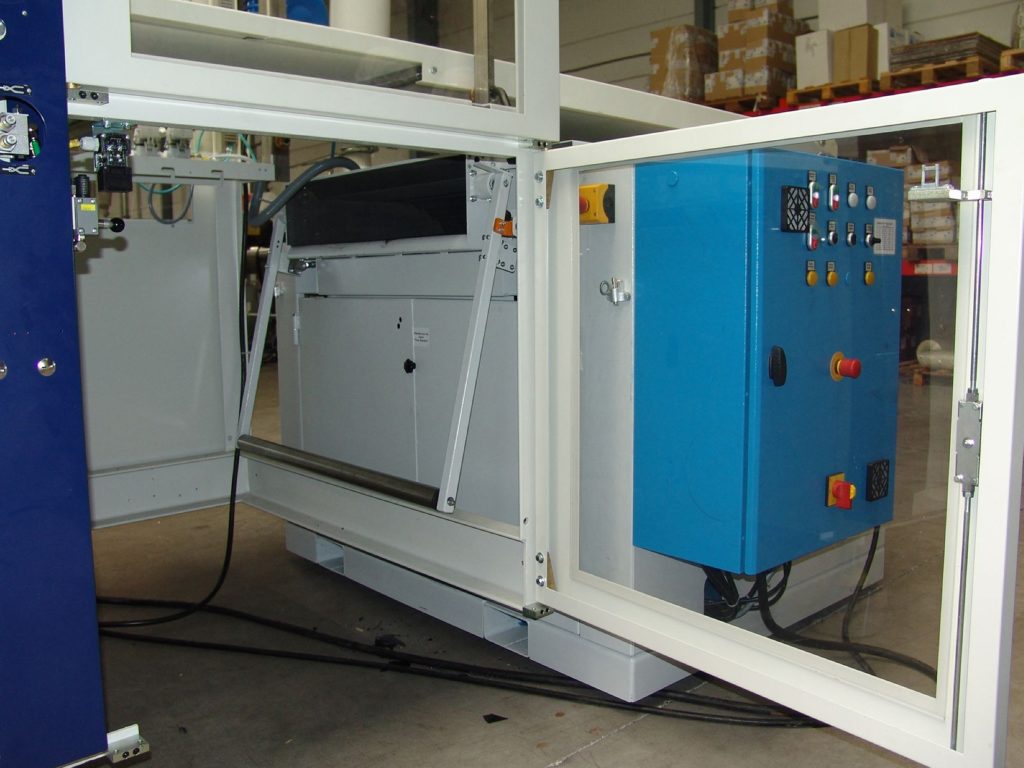
Individual features
- water cooled cutting chamber for temperature-sensitive material
- mechanical and electrical integration into a production line
- hopper for manual feeding of faulty parts
- low built version available
Technical specifications
Model | RS 2406-E | RS 2409-E | RS 30060-E | RS 30090-E | RS 30120-E | RS 30150-E |
---|---|---|---|---|---|---|
Rotor cutting diameter [mm] | 240 | 240 | 300 | 300 | 300 | 300 |
Infeed opening [mm] | 640 x 50 | 900 x 50 | 635 x 50 | 920 x 50 | 1.220 x 50 | 1.550 x 50 |
No. of rotary blades | 3 x 3 | 3 x 4 | 3 x 2 | 3 x 3 | 3 x 4 | 3 x 5 |
No. of stationary blades | 2 | 2 | 2 | 2 | 2 | 2 |
Motor power [kW] | 7,5 | 11 | 15 | 22 | 22 | 30 |
Throughput short term* [kg/hr] | approx. 230 – 350 | approx. 300 – 400 | approx. 350 – 500 | approx. 500 – 800 | approx. 700 – 1.000 | approx. 800 – 1.200 |
Throughput permanent* [kg/hr] | approx. 150 – 200 | approx. 200 – 300 | approx. 300 – 400 | approx. 400 – 600 | approx. 600 – 800 | approx. 700 – 900 |
Model | RS 38060-E | RS 38090-E | RS38120-E | RS 38150-E | RS 45090-E | RS 45120-E | RS 45150-E |
---|---|---|---|---|---|---|---|
Rotor cutting diameter [mm] | 380 | 380 | 380 | 380 | 450 | 450 | 450 |
Infeed opening [mm] | 635 x 70 | 920 x 70 | 1.220 x 70 | 1.550 x 70 | 880 x 70 | 1.180 x 70 | 1.480 x 70 |
No. of rotary blades | 3 x 2 | 3 x 3 | 3 x 4 | 3 x 5 | 3 x 3 | 3 x 4 | 3 x 5 |
No. of stationary blades | 3 | 3 | 3 | 3 | 3 | 3 | 3 |
Motor power [kW] | 22 | 22 | 30 | 37 | 37 | 45 | 55 |
Throughput short term* [kg/hr] | approx. 500-600 | approx. 600-900 | approx. 800-1.100 | approx. 700-1.100 | approx. 700-1.100 | approx. 900-1.200 | approx. 1.000-1.400 |
Throughput permanent* [kg/hr] | approx. 360-480 | approx. 480-700 | approx. 650-900 | approx. 850-1.000 | approx. 600-900 | approx. 800-1.000 | approx. 900-1.300 |
Options
Various rotor versions, drives and blade qualities are individually designed for your application, grinding reliably, energy-saving and producing an optimum grinding material quality.
Suitable wear protection packages secure your investment, reduce your maintenance costs and increase your profit when grinding abrasive materials.
Water-cooled cutting chambers and cooling-air supply reduce the thermal stress on your materials, protect against plastification in the cutting chamber and enable optimum grinding even in critical applications.
Maximum energy efficiency thanks to the latest design, drive motors in the energy efficiency class up to IE 4 and the use of GETECHA EnergySave, a system that significantly reduces your power consumption under partial load.
Electrical accessories from GETECHA connect your rotary cutter to the peripherals, control upstream and downstream units, create safety and increase your productivity. If you need special equipment and cannot find it anywhere, please contact us.
Perfect dosing and material feed into the rotary cutter as well as material discharge are options which are decisive for grinding performance and regrind quality. GETECHA peripherals (suction units, exhaust air dedusting system …) optimize your grinding system and create efficiency and safety.