The series RS 8000 has a cutting circle of 800 mm.
The RS 8000 is built in cutting widths of 900, 1.200, 1.500 and 1.800 mm.
Range of application:
- central granulator for bumpers, dashboards, skeleton film rolls, lumps from extruders, pipes, sheets…
- for voluminous parts as barrels or plastic fuel tanks
- for recycling applications for several tons/hr (plastic, copper, printed circuit boards)
Equipped with an automatic feed system and regrind transport, it becomes a high-performance granulating center.
We are looking foward to assist you on the choice of machine!
Advantages
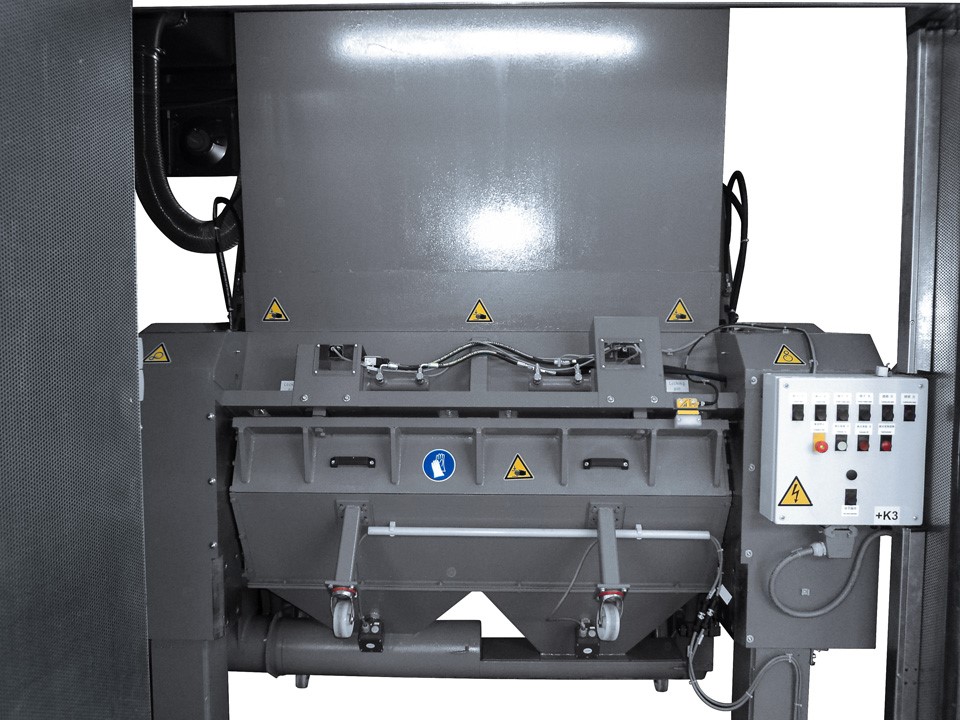
High efficiency,
excellent ergonomics
- opening of hopper and cutting chamber without tools
- screen cradle removable
- low cleaning time due to smooth, all-side machined surfaces
- high efficiency due to cutting geometry and EnergySave motor controller
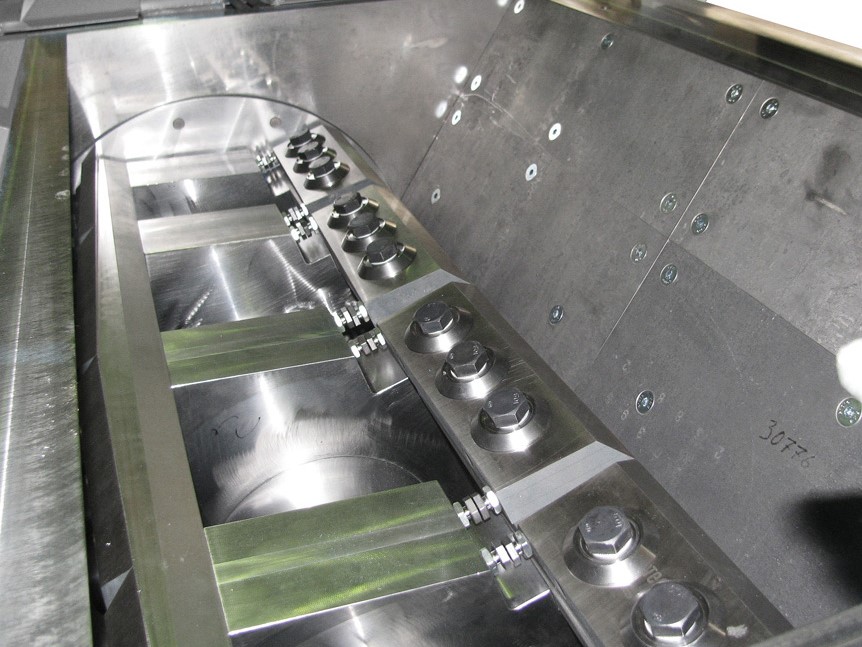
Excellent regrind quality
- scissors cut with constand cutting circle
- large screen surface enables high throughput rates
- rotary blades adjustable outside of the granulator
- short blades simplify handling
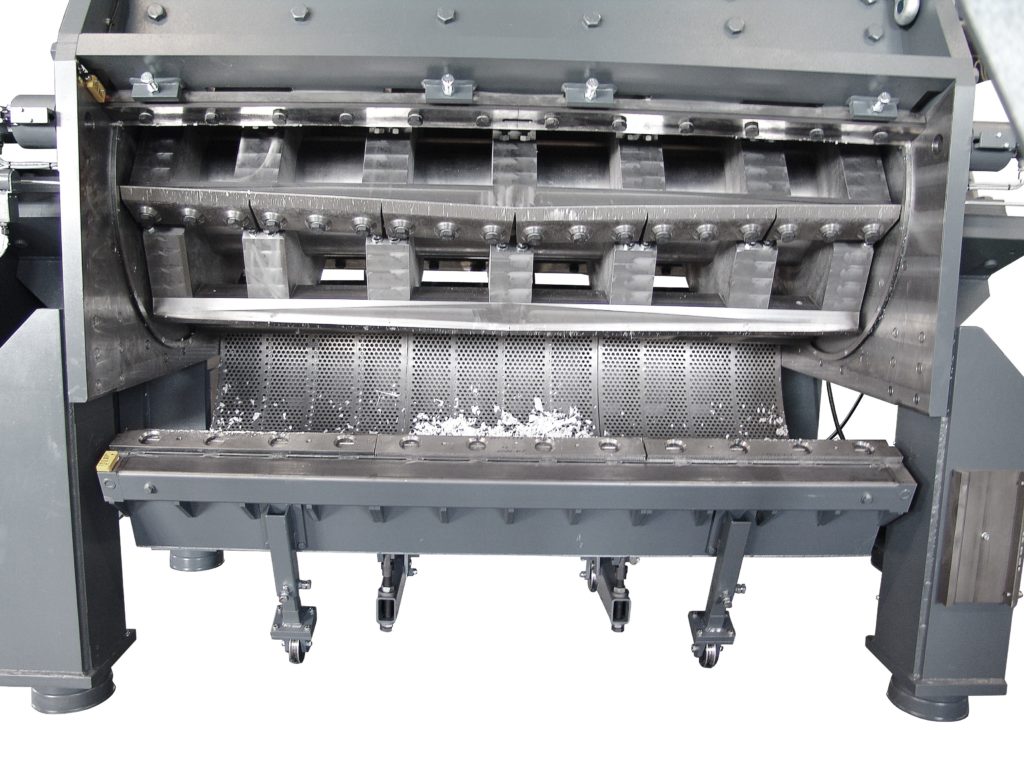
High reliability
- solid and torsion-resistant cutting chamber
- rotor shaft made of high-quality tempering steel
- rotor segments mounted on shaft with couplings (over 20 years experience)
- solid belt pulley for a high centrifugal moment
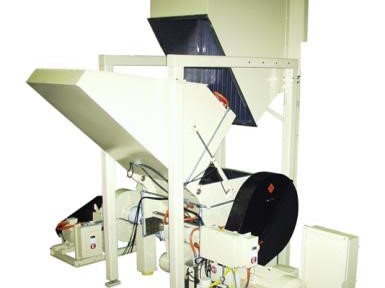
Individual features
- water cooled cutting chamber for temperature-sensitive material
- various hopper versions
- special rotors for a very wide variety of granulation tasks
- mechanical and electrical integration into a production line
Technical specifications
Model | RS 8009 | RS 8012 | RS 8015 | RS 8018 |
---|---|---|---|---|
Rotor cutting diameter [mm] | 800 | 800 | 800 | 800 |
Cutting chamber opening [mm] | 900 x 950 | 1.200 x 950 | 1.500 x 950 | 1.800 x 950 |
No. of rotary blades | 3 x 3 | 3 x 4 | 3 x 5 | 3 x 6 |
No. of stationary blades | 2 | 2 | 2 | 2 |
Motor power [kW] | 90 | 110 | 110 | 132 |
Throughput* [kg/hr] | approx. 600 – 1.800 | approx. 1.000 – 2.000 | approx. 1.200 – 3.000 | approx. 1.500 – 3.500 |
Dimensions
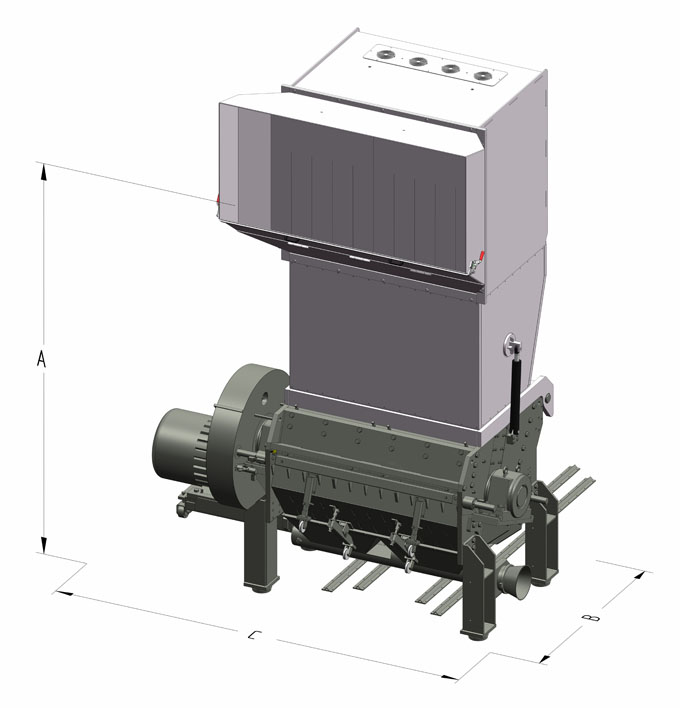
Model | A | B | C |
---|---|---|---|
RS 8009 [mm] | 2.810 | 2.075 | 2.970 |
RS 8012 [mm] | 2.980 | 2.075 | 3.270 |
RS 8015 [mm] | 3.150 | 2.075 | 3.570 |
Rs 8018 [mm] | 3.780 | 2.075 | 3.900 |
Options
Various rotor versions, drives and blade qualities of the model range RS 8000 are individually designed for your application, grinding reliably, energy-saving and producing an optimum grinding material quality.
Suitable wear protection packages secure your investment, reduce your maintenance costs and increase your profit when grinding abrasive materials.
Water-cooled cutting chambers and cooling-air supply reduce the thermal stress on your materials, protect against plastification in the cutting chamber and enable optimum grinding even in critical applications.
Maximum energy efficiency thanks to the latest design, drive motors in the energy efficiency class up to IE 4 and the use of GETECHA EnergySave, a system that significantly reduces your power consumption under partial load.
Electrical accessories from GETECHA connect your rotary cutter RS 8000 to the peripherals, control upstream and downstream units, create safety and increase your productivity. If you need special equipment and cannot find it anywhere, please contact us.
The modular granulator platform of the GETECHA rotary cutter RS 8000 allows variations of a wide range of proven assemblies, components and functions from the entire GETECHA rotary cutter range.
Perfect dosing and material feed into the rotary cutter as well as material discharge are options which are decisive for grinding performance and regrind quality. GETECHA peripherals (belt conveyor, screw feeders, metal detectors, ionizers, screw dischargers and extraction systems…) optimize your grinding system and create efficiency and safety.