The series RS 45000 has a cutting circle of 450 mm.
The RS 45000 is built in cutting widths of 600, 900, 1.200 and 1.500 mm.
Range of application:
- central granulator for injection moulding
- central granulator for blow moulding (jerrycans from 50 l)
- recycling applications (plastic, thin copper, printed circuit boards)
- infeed granulator for film or profiles
Advantages
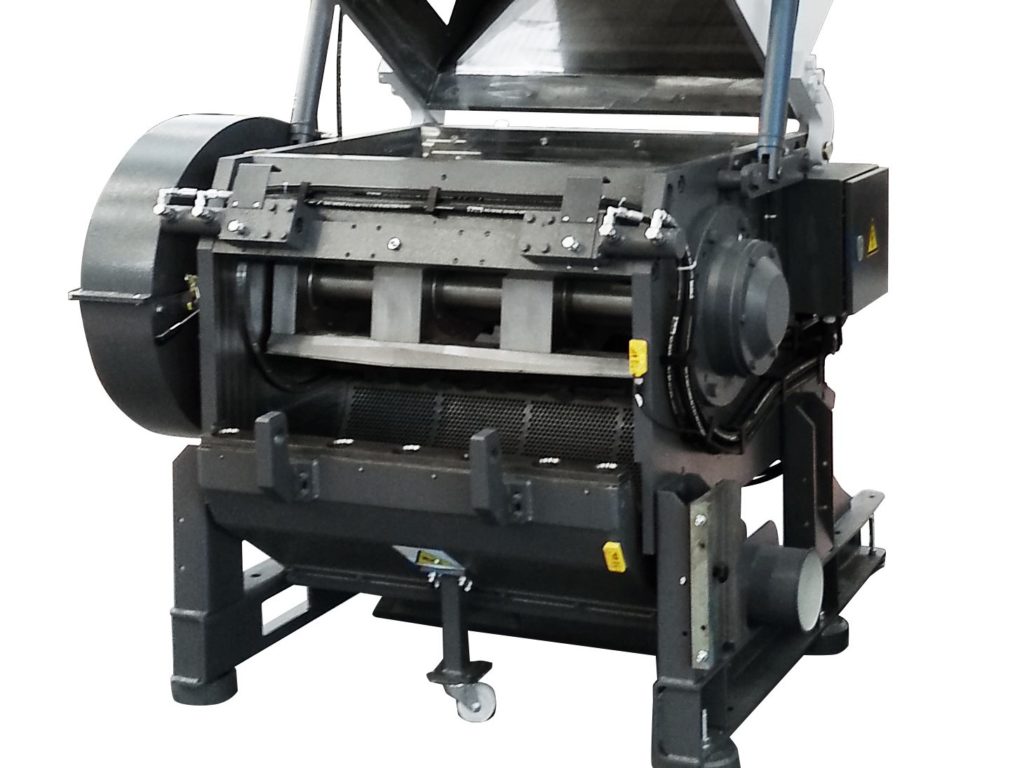
High efficiency,
excellent ergonomics
- opening of hopper and cutting chamber without tools
- screen holder removable
- low cleaning time due to smooth, all-side machined surfaces
- high energy efficiency due to cutting geomettry and EnergySave motor controller
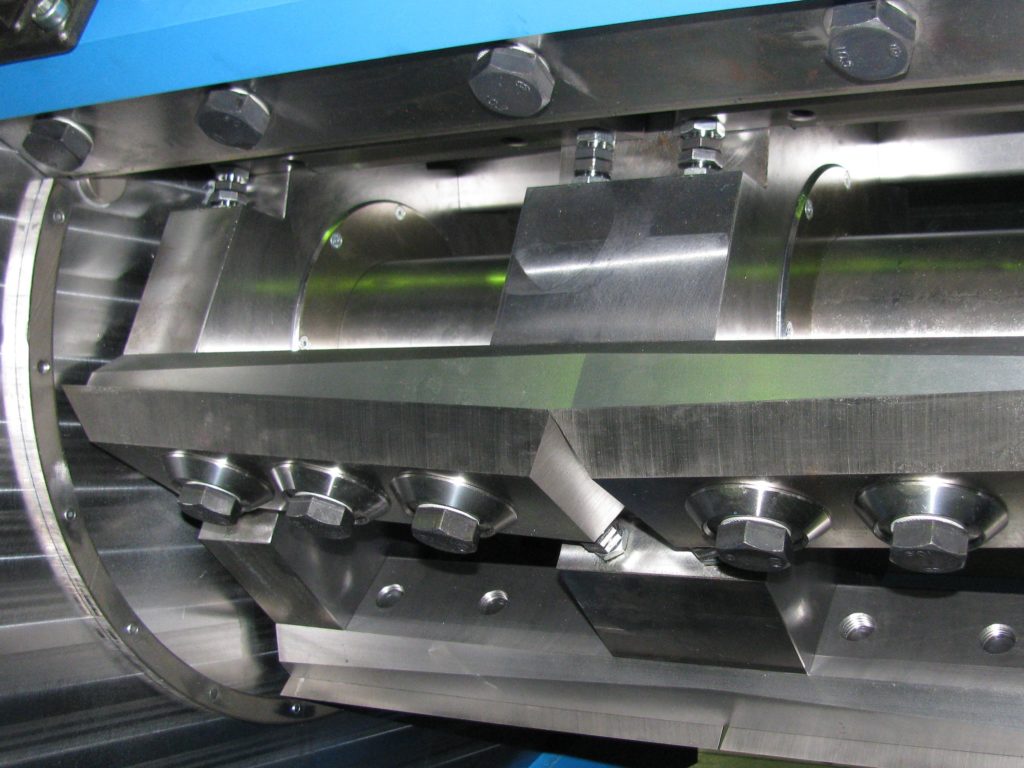
Excellent regrind quality
- scissors cut with constant cutting circle
- rotor in v-cut keeps the material in the centre
- stationary blade is mounted against hardened stop
- rotary blade adjustable outside of the granulator
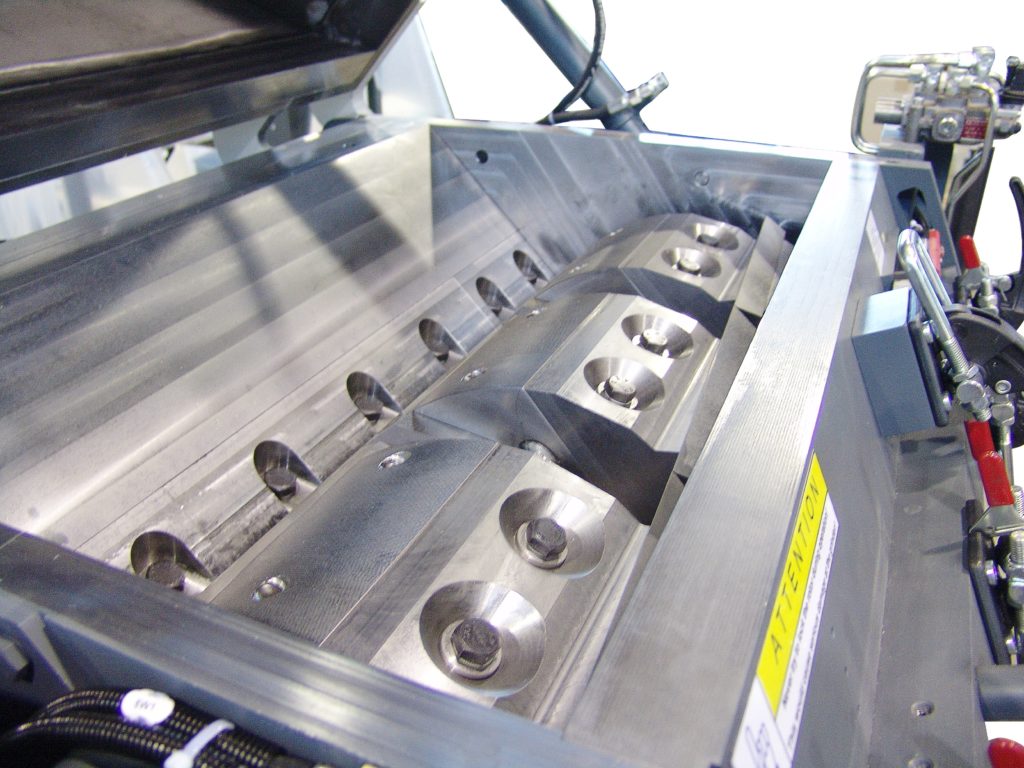
High realibility
- torsion-resistant cutting chamber
- rotor shaft made of high-quality tempering steel
- rotor segments mounted on shaft with couplings (over 20 years experience)
- solid belt pulley for a high centrifugal moment
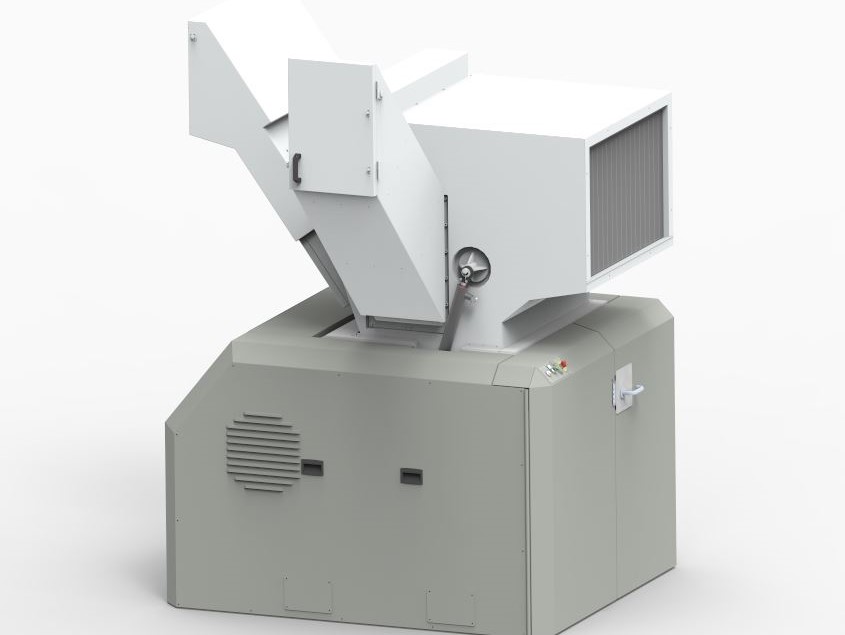
Individual features
- water cooled cutting chamber for temperature-sensitive material
- wear protected version for filled materials
- various hopper versions
- mechanical and electrical integration into a production line
Technical specifications
Model | RS 45060 | RS 45090 | RS 45120 | RS 45150 |
---|---|---|---|---|
Rotor cutting diameter [mm] | 450 | 450 | 450 | 450 |
Cutting chamber opening [mm] | 600 x 540 | 900 x 540 | 1.200 x 540 | 1.500 x 540 |
No. of rotary blades | 3 x 2 | 3 x 3 | 3 x 4 | 3 x 5 |
No. of stationary blades | 2 | 2 | 2 | 2 |
Motor power [kW] | 30 | 37 | 45 | 55 |
Throughput* [kg/hr] | approx. 500 – 800 | approx. 700 – 1.000 | approx. 900 – 1.200 | approx. 1.000 – 1.400 |
Dimensions
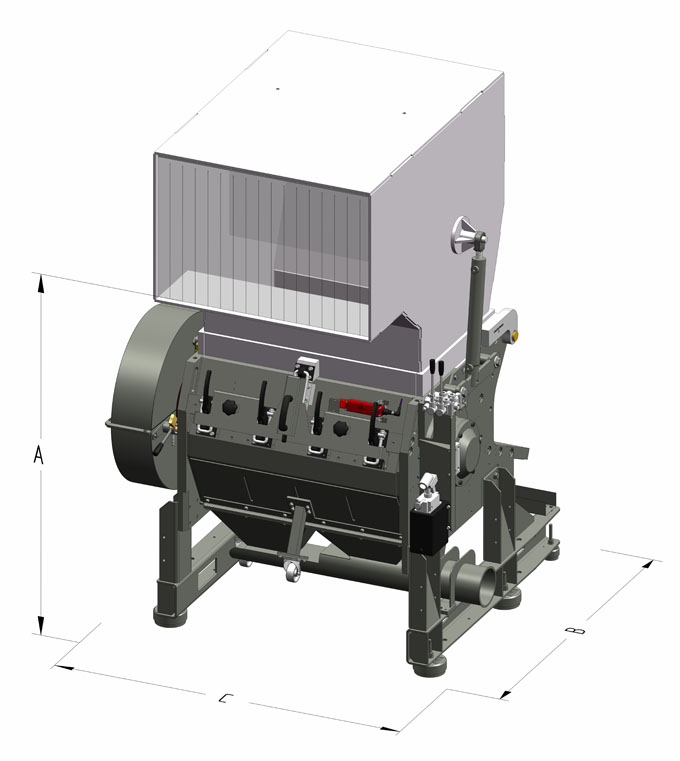
Model | A | B | C |
---|---|---|---|
RS 45060 [mm] | 1.560 | 1.680 | 1.190 |
RS 45090 [mm] | 1.560 | 1.680 | 1.490 |
RS 45120 [mm] | 1.560 | 1.680 | 1.790 |
RS 45150 [mm] | 1.560 | 1.680 | 2.090 |
Options
Various rotor versions, drives and blade qualities of the model range RS 45000 are individually designed for your application, grinding reliably, energy-saving and producing an optimum grinding material quality.
Suitable wear protection packages secure your investment, reduce your maintenance costs and increase your profit when grinding abrasive materials.
Water-cooled cutting chambers and cooling-air supply reduce the thermal stress on your materials, protect against plastification in the cutting chamber and enable optimum grinding even in critical applications.
Maximum energy efficiency thanks to the latest design, drive motors in the energy efficiency class up to IE 4 and the use of GETECHA EnergySave, a system that significantly reduces your power consumption under partial load.
Electrical accessories from GETECHA connect your rotary cutter RS 45000 to the peripherals, control upstream and downstream units, create safety and increase your productivity. If you need special equipment and cannot find it anywhere, please contact us.
The modular granulator platform of the GETECHA rotary cutter RS 45000 allows variations of a wide range of proven assemblies, components and functions from the entire GETECHA rotary cutter range.
Perfect dosing and material feed into the rotary cutter as well as material discharge are options which are decisive for grinding performance and regrind quality. GETECHA peripherals (belt conveyor, screw feeders, metal detectors, ionizers, screw dischargers and extraction systems…) optimize your grinding system and create efficiency and safety.