Sprues of all kinds and small faulty parts are ground economically and quietly – adapted to your granulation need. The large cutting chamber opening in combination with the angled rotor makes the size reduction of bulky sprues possible.
The GRS granulators can be equipped and adapted individually. Both models are available with low or high built frame. It is also possible to realize various rotor types or drive capacities.
Tell us your application needs.
Advantages
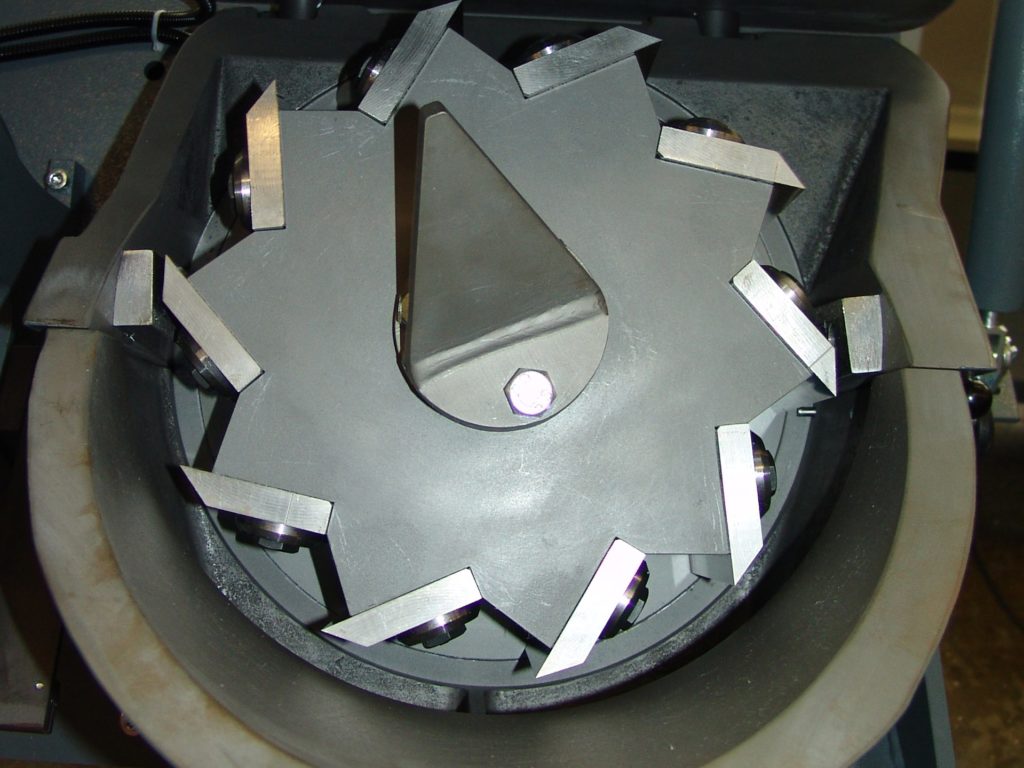
Quiet granulation
- divided solid cast cutting chamber reduces vibrations and thus noise
- hopper made of noise reducing composite material
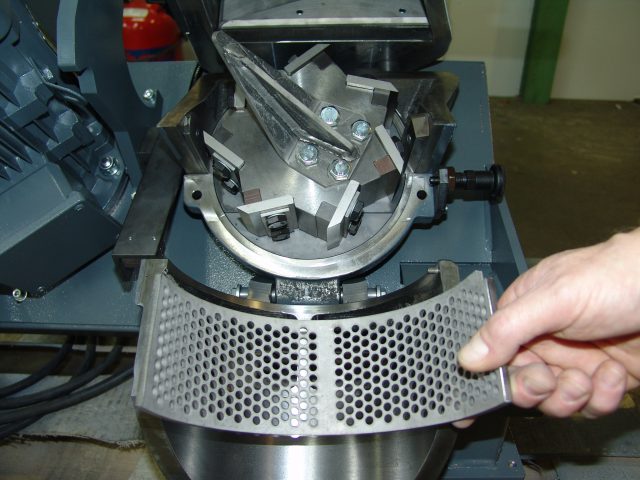
High productivity
- opening of cutting chamber without tools
- easy screen removal
- excellent access for fast and economical cleaning
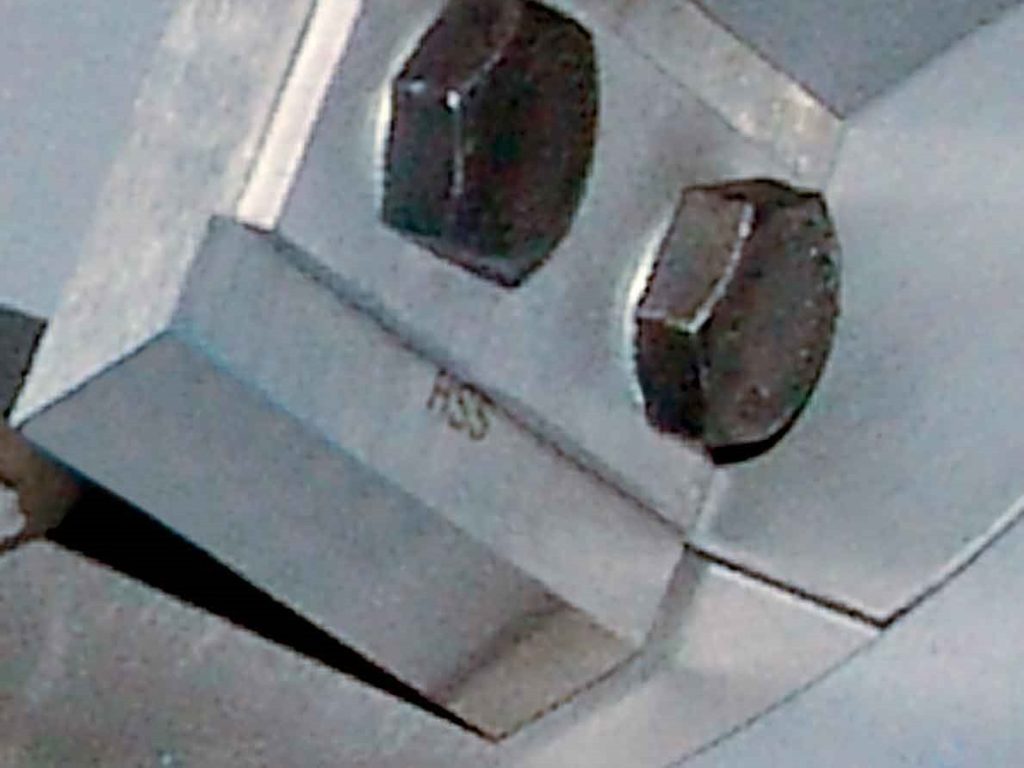
Excellent regrind quality
- self-cleaning steel plate
- low fines
- low rpm
- Highly consistent particle size
- easy to clean
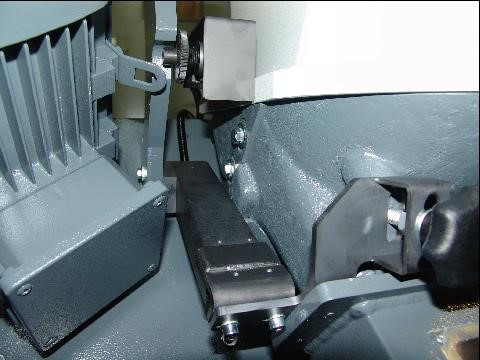
High reliability
- safety engineering according to performance level C
- starts even then hopper is full loaded
- W+T package prepares for highly filled engineered materials
Technical specifications
Model | GRS 180 | GRS 300 |
---|---|---|
Rotor cutting diameter [mm] | 180 | 300 |
Cutting chamber opening [mm] | 285 x 200 | 450 x 335 |
No. of rotary blades | 7 | 10 |
No. of stationary blades | 1 | 2 |
Motor power [kW] | 2,2 | 5,5 |
Throughput [kg/hr]* | approx. 35 | approx. 80 |
Dimensions
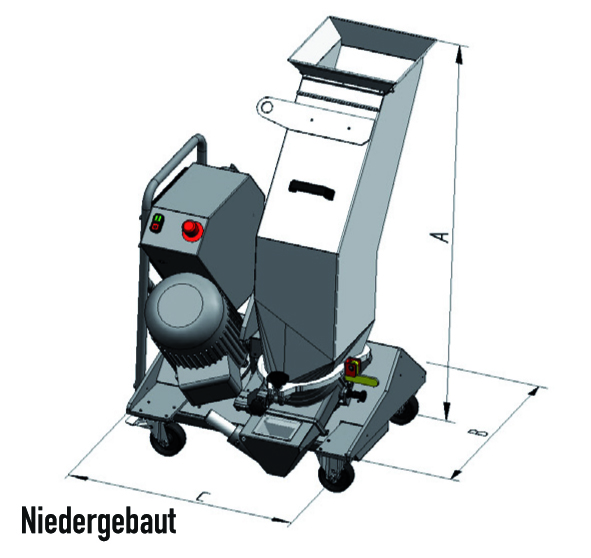
Model | A | B | C |
---|---|---|---|
GRS 180 [mm] | 1.220 | 665 | 710 |
GRS 300 [mm] | 1.600 | 900 | 930 |
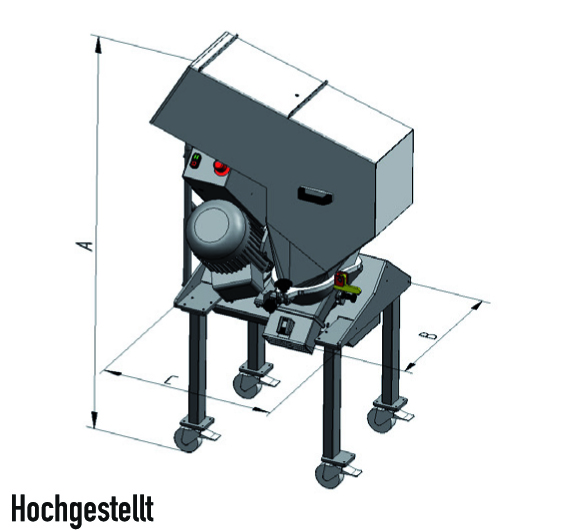
Model | A | B | C |
---|---|---|---|
GRS 180 [mm] | 1.660 | 665 | 710 |
GRS 300 [mm] | 1.960 | 900 | 930 |
Options
Various rotor versions, drives and blade qualities of the GRS series are individually designed for your application, grinding reliably, energy-saving and producing an optimum grinding material quality.
Suitable wear protection packages secure your investment, reduce your maintenance costs and increase your profit when grinding abrasive materials.
Water-cooled cutting chambers reduce the thermal stress on your materials, protect against plastification in the cutting chamber and enable optimum grinding even in critical applications.
The filling level of the material container is monitored to prevent overfilling of the container and material back-up into the grinding chamber. A warning signal can be issued or, for example, a vacuum conveyor can be controlled. The production process remains stable.
Whether with low or high frame, material container or free outlet, hopper for feeding by means of sprue picker or manually – the GRS series adapts to your production. An auger feeder to the position below the injection moulding machine or a flap hopper for production sensitive to cleanliness are available.