For a manufacturer of plastic containers, Getecha recently implemented a multi-station line for the fully automated packaging of new PET drinks bottles of various sizes. The line is directly linked to the production line and makes up to 6.000 bottles ready for dispatch per hour. Thanks to its modular design, Getecha can adapt the line flexibly to changing customer requirements by exchanging or adding individual stations.
Stacked on pallets ready for transport and wrapped in stretch film, the PET bottles come from the new packaging line of plant manufacturer Getecha. As the third complete solution in the meantime, it went into operation a few weeks ago at a German manufacturer of plastic containers. The fully automated multi-station line packages bottles with volumes from 200 ml to 1.5 L and is suitable for pallets in Euro (1.200 x 800 mm) and industrial dimensions (1.200 x 1.000 mm). It is docked directly to the stretch blow molding machines of the bottle production and is designed for an hourly output of up to 6.000 PET bottles. Based on its modular concept, Getecha can replace, remove or add to the individual stations of the packaging line at any time and thus adapt at short notice to special orders or special series of the customer. All mechanical interfaces and the control technology (PLC) are adapted to this.
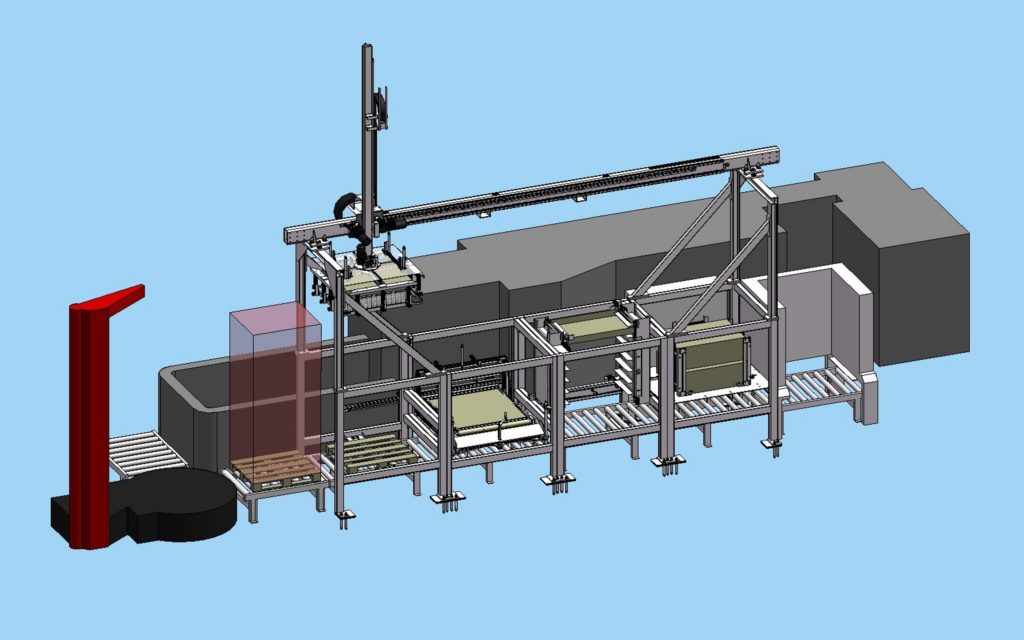
Customer-specific system solution: Getecha multi-station line for automated packaging of PET drinks bottles (Illustration: Getecha).
Five stations on three levels
Via its modules, the Getecha packaging system brings together pallets, packaging materials and PET bottles in a process-safe manner. In terms of design, the approximately eight-metre long line consists of three material flow technology functional levels: A multi-driven heavy-duty roller conveyor that connects all stations linearly with each other (level 1); the five stations pallet dispenser, tray magazine, storage table, palletizing unit and stretch wrapper (level 2); and a handling device that travels over four stations (level 3).
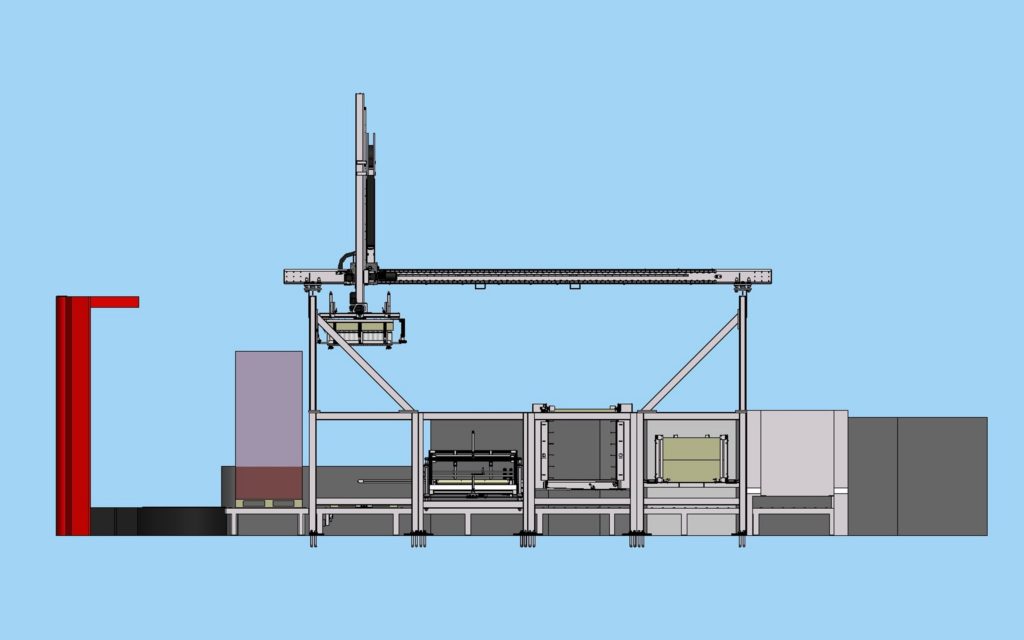
Fast and flexible: The fully automated multi-station system packs bottles with volumes ranging from 200 ml up to 1l5 l and is suitable for Euro- (1.200 x 800 mm) and industry-size (1.200 x 1.000 mm) pallets (Illustration: Getecha).
The process chain starts at the pallet dispenser, which has a capacity of up to 15 pallets; the automatic stacking of the pallets is controlled by the PLC of the system. The tray magazine feeds the individual trays according to the paternoster principle. In the storage table, the bottles are automatically transferred from the production; here the bottles run in rows over a conveyor belt against a two-stage stop, which also allows for offset positioning of the bottle rows. Clocking is carried out continuously row by row, which later avoids back pressure in the layer and increases process reliability when handling demanding bottle geometries. The complete rows are then pushed onto the layer table. As soon as a layer is complete, the handling device on the third level of the line comes into play: In line with the cycle of the line, the two-axis servo system with its combination gripper picks up the layers of bottles from the table and stacks them in the adjacent palletizing station with millimeter precision on the previously precisely aligned pallet. At the same time it also positions the interlayer cartons and the carton lid.
Stacked, wrapped, secured
The accurately fitting stacked packaging unit finally reaches the stretch winder, which secures it against slipping and damage. The final step is an integrated labelling system with printer, which can also be controlled via the line’s PLC. And if PET bottles are to be fed from several production lines simultaneously, Getecha offers the option of equipping the packaging line with an additional buffer station.
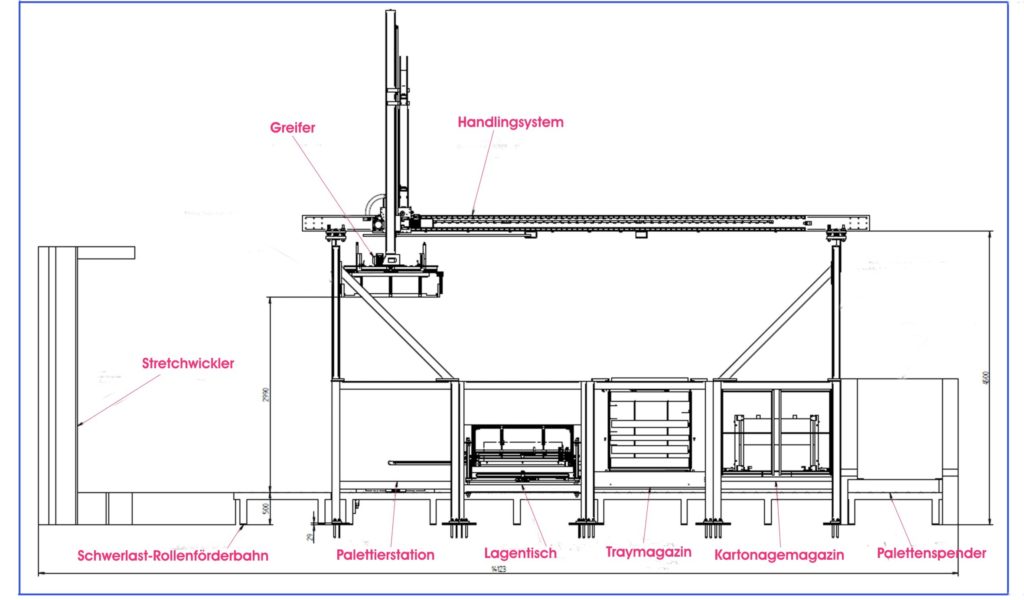
Modular plant concept: Getecha can exchange the individual stations of the packaging plant at any time, remove them or enhance them such that it is possible to customize for specific orders or production runs at very short notice. (Illustration: Getecha)
This fully automated and modular multi-station line was already the third packaging line that Getecha supplied to the customer from the beverage industry as a complete system solution from one source. As with other projects of this kind, the range of services provided by the Aschaffenburg-based plant manufacturer extended from project planning and design, engineering, programming and assembly to commissioning. In the role of service partner, the company also takes care of maintenance and repair.
Press release May 2011
Packaging technology / automation / material flow / plastics technology / food industry