Horizontal granulator as process step for the production of lightweight granulates
High-strength rigid foam materials are an important material-relevant component for the realisation of modern lightweight constructions for the aircraft and automotive industry as well as medical technology. Their production is based amongst others on the processing of high-quality plastic granulates from extruded copolymer semi-finished products. By reading this, you will learn why the use of a customised granulation solution from the German plant construction company Getecha represents a central process step of their generation.
The realisation of light but highly stressable sandwich constructions for the aviation and automotive industry is one of the typical areas of application of rigid foams made of polymethacrylimide. One crucial component for their production is the thermal processing of high-quality plastic granulates with defined grain sizes. These granulates are generated through targeted and repeatedly accurate mechanical granulation of hard copolymer panels. This takes place in high-performance granulators specifically designed for this purpose, as realised by the German company Getecha – most recently for example for one of the leading rigid foam producers. In this case, the plant engineering company used a granulator of type RS 38060 from its successful RotoSchneider range as the technical basis for this purpose, which was designed as special HZ version. This means: This granulator has a number of customer- and application-specific features and system components beyond the serial model, which enable an economical and calculable production of copolymer granulate with defined grain size – in this case, between 0.5 and 3.0 mm. The generation of a proportion of ground material as low as possible in the range of < 0.5 mm is regarded as a guide value here. Below this value, the granulate can only be processed in a limited way.
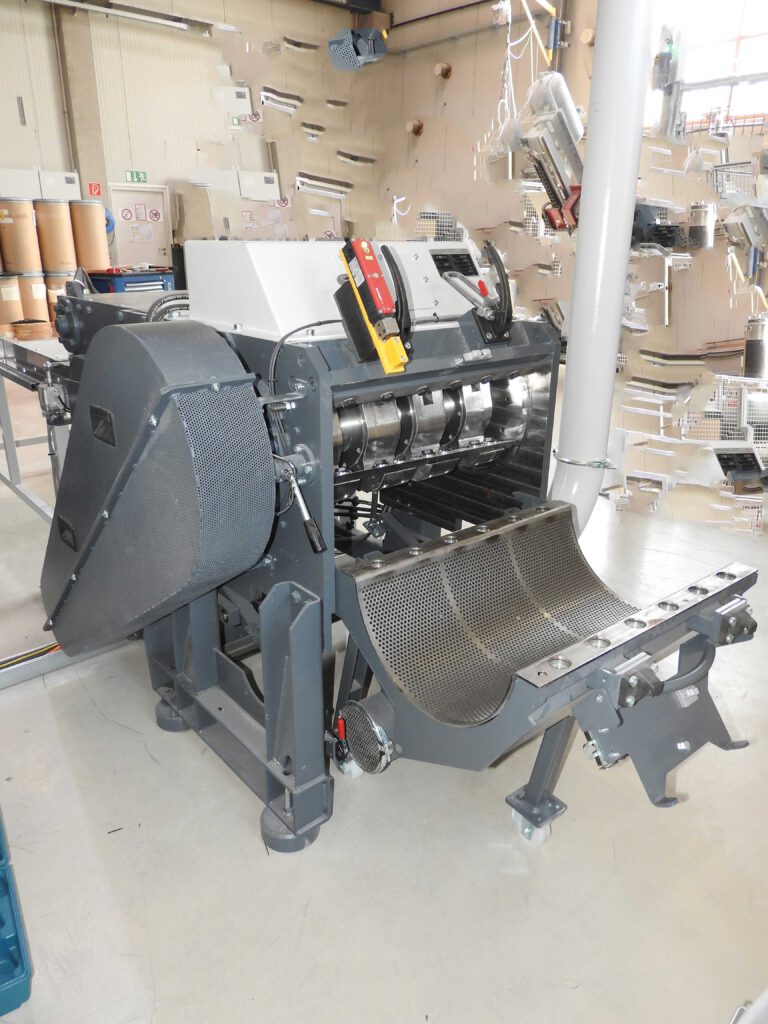
Photo 1: Generates copolymer granulate with grain sizes between 0.5 and 3.0 mm: The scissor-cut granulator RS 38060 HZ of the Roto-Schneider range from Getecha – here with opened screen carriage.
Getecha Engineering placed special attention on the provision of a maintenance-free complete solution, which also includes the required extraction equipment and a customised feed system in addition to granulation. Crucial for this: A horizontal granulator design (HZ) enabled integration of a powerful double infeed pair of rollers. “As a result, the material feed can take place horizontally, which has the advantage that the user can freely determine the infeed speed as well as the length of the first cut of the panels and profiles to be granulated. In combination with a granulator screen with suitable hole dimension – a raised screen with hole sizes between 3.0 and 5.0 mm – our system solution generates a high proportion of granulate of the desired dimensions with at the same time minimum fine portion”, says Eva Rosenberger, Sales Manager and shareholder of Getecha.
Project work with three field tests
The mostly automated complete work is the result of a multi-level development and optimisation process of the customerin cooperation with Getecha, with different granulator feeds with frontal and rear hoppers of traditional design being tested and analysed in the process. The unregulated material feed induced higher energy consumption here, and the ground material dimensions could not be directly influenced. Furthermore, the manual panel feed of the bulky panels weighing up to 30 kg proved to be impractical.
Against this background, the engineering team from Getecha decided to use the horizontal design of the HZ design. With the horizontal feed, the panels or profiles to be granulated can be positioned ergonomically at work height in front of the system on a feed table. The controlled infeed occurs automatically on the cutting plane of the grinder frequency-controlled and with controlled infeed speed via a double roller infeed pair directly into the granulator rotor of the RS 38060 HZ granulation system. The top infeed roller pair of this tandem is balanced on a hydraulic rocker, and can be set in the pressing force. Both rollers are knurled and can be reversed.
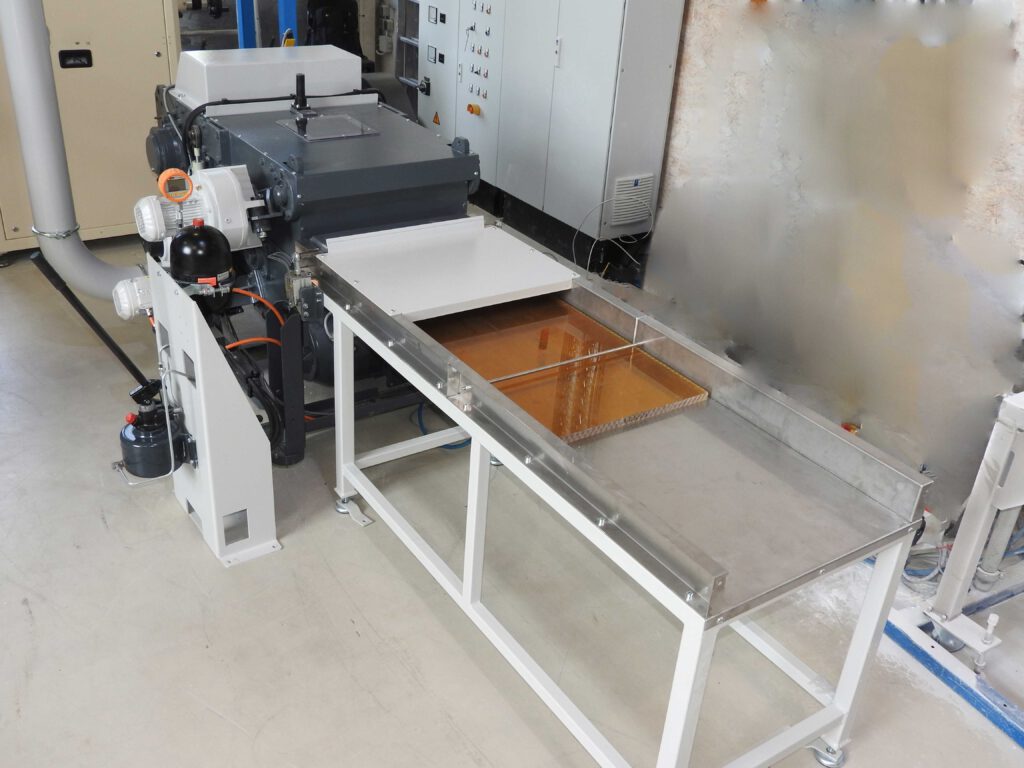
Photo 2: Complete solutionfor the production of high-quality plastic granulates from extruded copolymer semi-finished products: Getecha granulator RS 38060 HZ with integrated double roller infeed pair, feed table and extraction system.
Sustainable and energy efficient
This smart construction offers a whole host of advantages and provides the entire process with a clear boost to innovation. This is not only because the panels and profiles to be granulated can be safely and easily placed and positioned on the feed table, but mostly because the material feed now occurs in a controlled way, automatically, safely and with the roller feed at perfect height between rotor and stator knife – without manual intervention.
Another crucial factor for the efficient operation and optimum system integration of a powerful granulation tool such as the RS 38060 HZ is its communication with the periphery and sensors. Specifically, this means: The granulation process only starts once the required release signals from the material extraction have been captured, as well as additional units required for the subsequent processing. The following is also important: The user can freely choose the length of the first cut. For this purpose, the system calculates the optimum infeed speed from rotor speed, number of rotor blades and feeding speed. Thanks to the combination of controlled material feed and overload protection, a harmonious first cut length is achieved – with at the same time minimum fine portion in the ground material and highest cutting performance. This noticeably contributes to increased efficiency: The connected load decreases from 30 to 22 kW and the maintenance effort lessens.
Flexibility and ergonomics
The complete solution from Getecha not least provides users with a high degree of flexibility, as they can directly make an impact on the quality and dimensioning of the ground material via the selected screen size diameter, the rotor speed and the feed of the double roller infeed pair. Instead of a feed yable, handling systems or conveyor belts can also be used for the material feed. Rotor diameters of up to 800 mm can be used for the processing of thicker panels. For the secondary grinding of pre-granulated materials from recycling or for wet grinding, there is the option to integrate a large frontal charging hopper instead of a double roller infeed pair. The material to be granulated is fed to the grinding chamber via feeding screws.
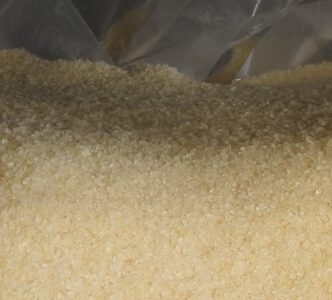
Photo 3: In coordination with the subsequent processes, the granulation system from Getecha produces between 150 and 200 kg plastic granulate per hour. The screen size diameter and feeding technology were adapted precisely to these specifications.
In addition to the easy handling, further advantages of the system solution are the optimum ergonomics. The double roller infeed pair prevents material particles from spurting out, and the noise emissions of the granulation system are significantly lower than for hopper granulators due to the small opening gap between the infeed rollers. Like all RotoSchneider rotary cutters of the Getecha series RS 38XXX bis RS 8018, the RS 38060 HZ can also be additionally equipped with integrated sound protection or sound insulation cabins.
As indicated, the complete solution from Getecha includes an integrated exhaust air system – in this case a GA 500-S with cyclone separator from the company’s range. In addition to the extraction, it comprises a ground material dosing and is designed in such a way that the ground material is transported with clean and dosed extraction via a rotary feeder to the material forwarding without transport through the material transport blower. The granulation system is operated with a vacuum here.
Saving resources, lowering costs
For the purpose of optimum process harmonisation with the subsequent periphery, the specification sheet of the rigid foam manufacturer intended that the granulation performance of the new granulation station should be between 150 and 200 kg/h. Screen size diameters and feeding technology were adapted accordingly. However, Eva Rosenberger stresses “that the performance of the system can be increased to up to 600 kg/h if required”. In general, the RotoSchneider rotary cutters of the HZ series are suited to a granulation performance of up to 3,000 kg/h. For this reason, when using a frontal charging hopper with screw feed, they provide a compact, powerful alternative to traditional granulator designs for the recycling of pre-granulated materials as well.
With the RotoSchneider granulators as well as a selection of guillotine shears and foil cutters, Getecha is able to realise customised system solutions for material granulation and return close to production for throughputs between 10 and 5,000 kg/h. As demonstrated with the granulation station for rigid foam production, the portfolio of the plant construction company also comprises suitable feed, materials handling and extraction technology. The fact that the development of such complete solutions leads to material and handling tests via several iteration levels and alternative construction approaches is part of day-to-day business. Eva Rosenberger also points out that “a requirement analysis with a calculation prognosis for the costs and consumption occurs in advance of each project”, to ensure the profitability and efficiency of each complete solution.”