With the objective to create more space for its production and to centralise the entire granulation technology, the packaging material manufacturer Pro-Pac established a new hall at the Vechta site two years ago. In time, more and more granulation machines for the processing of residues and faulty parts from different thermoforming and extrusion processes moved in. From the start, the focus was on several automated complete solutions from the company Getecha, headquartered in Aschaffenburg.
The provision of user-friendly products for the packaging, protection and presentation of fresh foods has become the mission of plastics processor Pro-Pac. With a continuously expanding range of packaging items made of polypropylene, polyethylene as well as biodegradable PLA (lactic acid / cornflour), the company has been steadily growing since 1988. The plates, cups, bowls, mugs, boxes and trays are predominantly produced in fully automatic extrusion and thermoforming lines at the headquarters in Lower Saxony Vechta. For technical reasons, there is a significant amount of residues, faulty parts and samples resulting from this type of large-scale production, but Pro-Pac is consistently having these granulated, prepared and recycled.
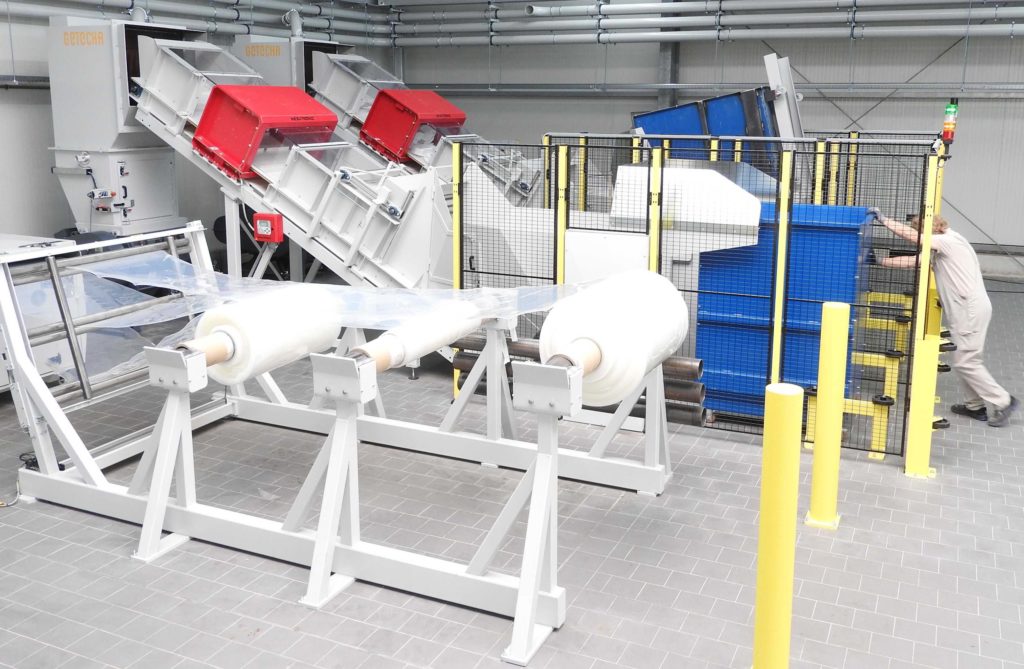
In order to be able to organise this circulatory system as efficiently as possible and directly on site, and at the same time create space for additional process optimisations in the production, the management decided on centralising the granulation technology about three years ago – and a new hall was built specifically for this purpose. It went operational in 2016 and provides space for up to six automated lines for the granulation of production and start-up residues.
View into the new granulation centre from Pro-ac: A section of the Getecha granulator for PP film residues of different thickness can be seen in the foreground; behind are the two Getecha lines for the granulation of stacked thermoforming residues.
High degree of automation desired
In order not to lose any time when project planning suitable granulation and automation systems, please contact the responsible Pro-Pac Plant Managers Johannes Tegenkamp and Kurt Wördemann at Getecha in Aschaffenburg before the construction phase. “We have been in partnership with the Franconian granulator manufacturer for some time; we have been using some rotary cutter granulators from Getecha for many years to granulate edge trims and blanking skeletons. We also knew that Getecha as special machine builder is able to handle complex automation projects”, says Kurt Wördemann. This aspect in particular was of high relevance for both plant managers, as Johannes Tegenkamp explains, the new processing centre does “not serve granulation for the sake of granulation, but predominantly the largely automated and efficient production of materials and their complete return to production.”
With this objective in mind, a meeting was arranged at the end of 2016 with Andreas Lanz, the responsible Area Sales Manager of Getecha. The plans envisaged the installation of initially two lines in the first project phase for the granulation of stacked thermoforming parts from series production of white and transparent PP and PET containers, as well as a third line for granulating PP film residues of different thickness. In all three cases, the result was to be a complete solution. It was thus not only important to select the right hopper and infeed granulators, but to also plan the complete input and output technology. As expressed by Andreas Lanz as follows: “The task formulation from Pro-Pac was complex. It included the process-technical integration of customer-specifically modified granulators into an environment of conveying and handling technology, metal detectors, exhaust air purification as well as filling and packaging technology – naturally, including the control- and safety-related integration of all components.” The factors of energy efficiency and ergonomics were also very important for Pro-Pac.
Conveying, tilting, granulating…
For the granulation of the thermoforming parts, two Getecha granulators of type RS 45090 were chosen. These modern hopper granulators are designed for throughputs of up to 900 kg/h and optionally also have granulator housings with highly effective sound insulation. Due to their drive positioned at the top and integrated into the housing, they are compact and only require a relatively small footprint. In principle, an RS 45090 can be equipped with additional bypass hoppers for the simultaneous feeding of tubes, profiles and panels. It can thus be used very flexibly. In addition to the high overall stability of the granulator, a prerequisite for this flexibility is its powerful 3-blade rotor – it takes in voluminous plastic residues very well – and the use of two stator blades in the grinding chamber. A hydraulic opening mechanism facilitates access to the sieving tray, and an electrically monitored rotor blockade turns routine blade changes into a simple and safe affair. Tailored to their application at Pro-Pac, the granulators received a fixed hopper with a large access door. This saved additional space.
At Pro-Pac, the RS 45090 forms the granulation-related core of two multi-level processing lines operating in parallel. “As for many similar projects, again the fundamental objective here is to cleanly and quickly guide faulty parts made of PP and PET – predominantly plates delivered in stacks of 250 mm diameter – from collection containers to the granulators. This has to be as dust-free as possible and without clogging the conveyor or mill hopper, ensuring an error-free and efficient continuous production process”, says Getecha Manager Andreas Lanz.
“Homogeneous material throughput”
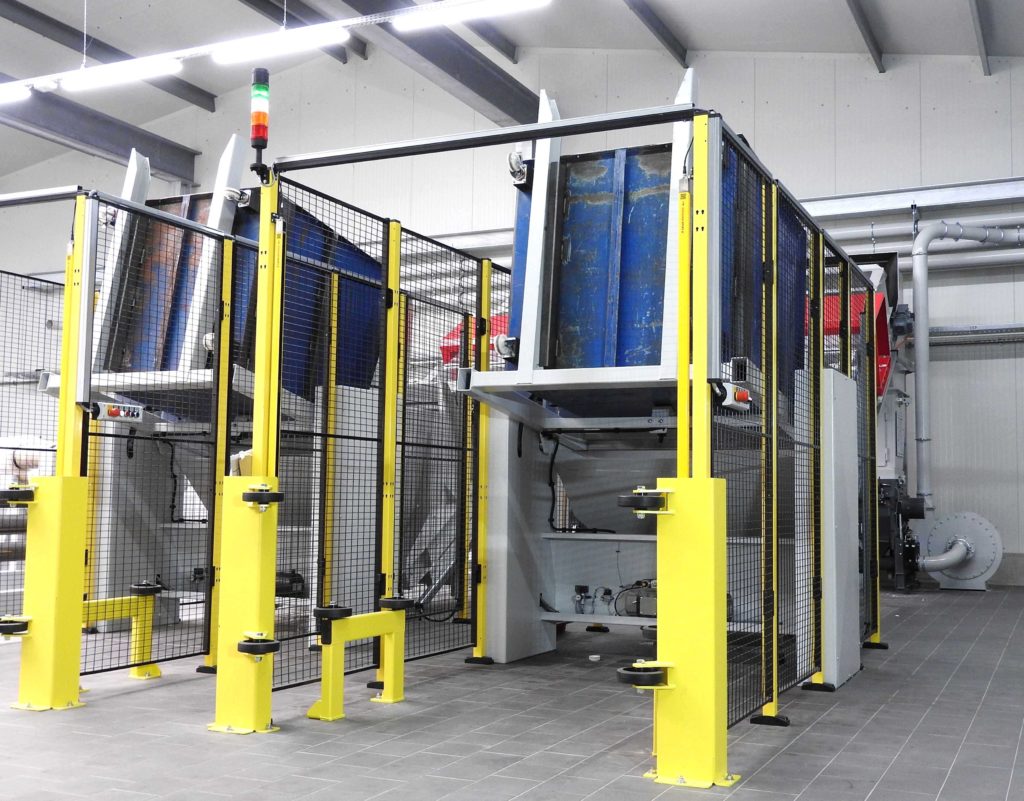
Getecha designed the starting point of the process as security gate with fully automatic tipping device. Here, the collection containers are rolled from production into suspension position by an employee, and tipped fully automatically into a transfer hopper – at up to approx. 132° and until the defined degree of discharge is achieved. An integrated vibration system can be added as support. The container is then lowered again, removed and rolled back to series production. “Getecha has adjusted the entire tipping and emptying process so that we can use our own roller boxes, meaning we did not have to purchase new containers especially”, says Pro-Pac Plant Manager Kurt Wördemann. From the transfer hopper, the drinking cups, plates and bowls get to a conveyor, whereby a driven stripper roll separates faulty parts stuck to one another. Also important: “As the collection containers are coming directly from production, they may contain metal parts, which will damage the systems as well as contaminate the ground material. To prevent this, a tunnel detector is located above the conveyor with double-layer metal detection coil, which reliably detects all metallic particles and – if required – interrupts the supply”, says Andreas Lanz of Getecha. This way, it is ensured that there is a homogeneous and continuous material flow in the direction of the granulator hopper.
For the environment of the granulating line to remain clean, Getecha has encased the conveyors on all sides with a transparent plastic cover. So no material can fall off the conveyor. However, flaps above and below the metal detector enable easy access to the conveyor, for example for manually removing metallic interfering parts. Mostly separated, the material finally falls into the hoppers of the two RS 45090 and is granulated in their grinders to particles with diameters of 6 mm.
Process reliability and energy efficiency
Typical for the granulation solutions from Getecha is the integration of numerous features, which serve process reliability as well as energy efficiency. To prevent the granulators from being overloaded in case of particularly high material output, the company equipped the Pro-Pac lines for example with its LAS system for a load-dependent timeout of the material feed. Andreas Lanz explains: “The control permanently requests the current consumption from the granulator. If a previously defined limit value is exceeded for too long, the belt conveyor switches off temporarily. Once the electricity requirement decreases, it picks up speed again – all this occurs automatically.” The fill-level monitoring of the granulators has the same effect. In this case, it is the light sensors reporting to the control when the hoppers are at risk of becoming full. The feed also downregulates in this case and adjusts to the material output and spontaneous volume peaks which can occur if high stacks with thin-walled faulty parts only disintegrate in the hopper. “Many older granulators of other makes lack the intelligent control functions of our rotary cutter series. This results in blockages and bottlenecks in the material flow. The entire process then needs to be stopped and the granulator needs to be emptied. All this is not really in keeping with the times”, says Andreas Lanz of Getecha.
For Kurt Wördemann of Pro-Pac, the Energy Save System (ESS) is also a real advantage. Getecha has been equipping almost all larger rotary cutter models with it for just over three years. “This function decreases the power consumption of the granulators under partial load and when idling. In addition, the soft start-up of the ESS prevents damaging current spikes in the startup phase, which also preserves all mechanical components”, says the plant manager. Ultimately, this not only results in a good energy balance of the granulators, but reduces the maintenance costs at the same time.
From the roller block to the double infeed system
An overload cut-off device as well as the innovative Energy Save System from Getecha can also be found in the infeed granulator RS 3012 E, which is at the core of the third granulating line in the processing centre of Pro-Pac. What was important for Andreas Lanz here was to plan a system solution where up to three rollers with PP film residues from thermoforming were to be fed into an efficient granulation. “Various variables had to be considered here, as the film thicknesses vary between 0.2 and 1.2 mm, and the widths and diameters of the rollers also change constantly”, says the Getecha manager. So with the RS 3012 E, Andreas Lanz could provide customers with an infeed granulator which thanks to its high degree of automation was ideal for this task.
The RS 3012 E is representative of an infeed granulator series from Getecha, which has been setting standards for years with regard to the granulation of entire sheets, edge trims and blanking skeletons from thermoforming. The rotor of these machines has a cutting circle of 300 mm and is operated as standard with cutting lengths between 410 and 1.575 mm. The roller infeeds have widths between approx. 100 and 1.550 mm and are available in various versions. For safe operation with very different performance requirements, Getecha is also offering several systems for regulating the infeed speed.
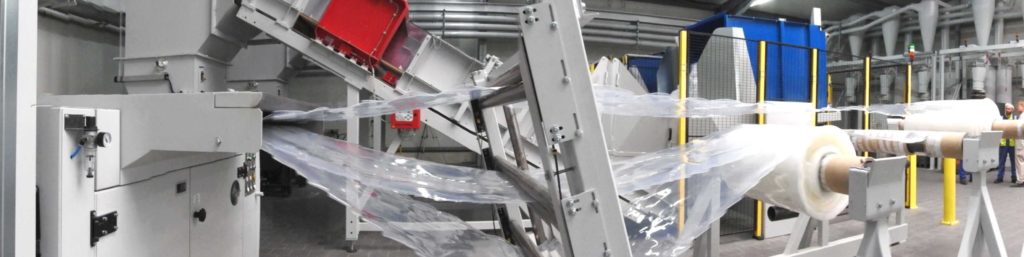
If you were standing in the processing centre of Pro-Pac now and were looking at this granulating line, you would see a rotary cutter infeed granulator version with particular wear protection and double infeed system, via which films of different thickness can be fed at different speeds. A phalanx of three roller blocks of different heights is positioned in front.
Here, the forklifts approaching from the production set down the rollers with the surplus film. An employee then guides the beginning of the film through the film end detection to the feed slot of the granulator. Everything else occurs automatically. Andreas Lanz explains: “The number of roller blocks actually being used is detected by a sensor and reported to the RS 3012 E, whereby the film end detection also activates here. And because the infeed of the granulator reverses as soon as the film end is detected, the system enables simultaneous infeed of all required beginnings of film. This way, we optimise the material flow even before granulation.”
Automatic speed control
The actual granulation process of the RS 3012 E is then markedly smooth and balanced – not least because the granulator used at Pro-Pac has a new, intelligent system for the speed control of the infeeds for offline granulation of extruded films. This development from Getecha provides the possibility to automatically adjust the infeed speed of several simultaneously infed films – depending on the performance required for granulation and at the same time under consideration of the ground material volume which fluctuates depending on the film thickness. The rotor speed of 420 rpm as well as a special sieve with drilled punch holes at an angle counteract the formation of unwanted long parts in the ground material even with a slow infeed. “A floating roller control system with dancer arm has proven itself for many years for this purpose, synchronising the speed of the infeed with the speed of the film system and controlling the tensile load of the films. However, our new solution works more accurately, is more compact, and ensures an optimum throughput above all and very high ground material quality”, Andreas Lanz explains. Alternatively, the infeed speed can always also be preselected manually. Furthermore, Getecha fundamentally offers a whole series of different control systems for its infeed granulators for adapting the infeed speed – for inline granulation behind the extrusion line or for the granulation of edge trims.
Fresh ground material for production
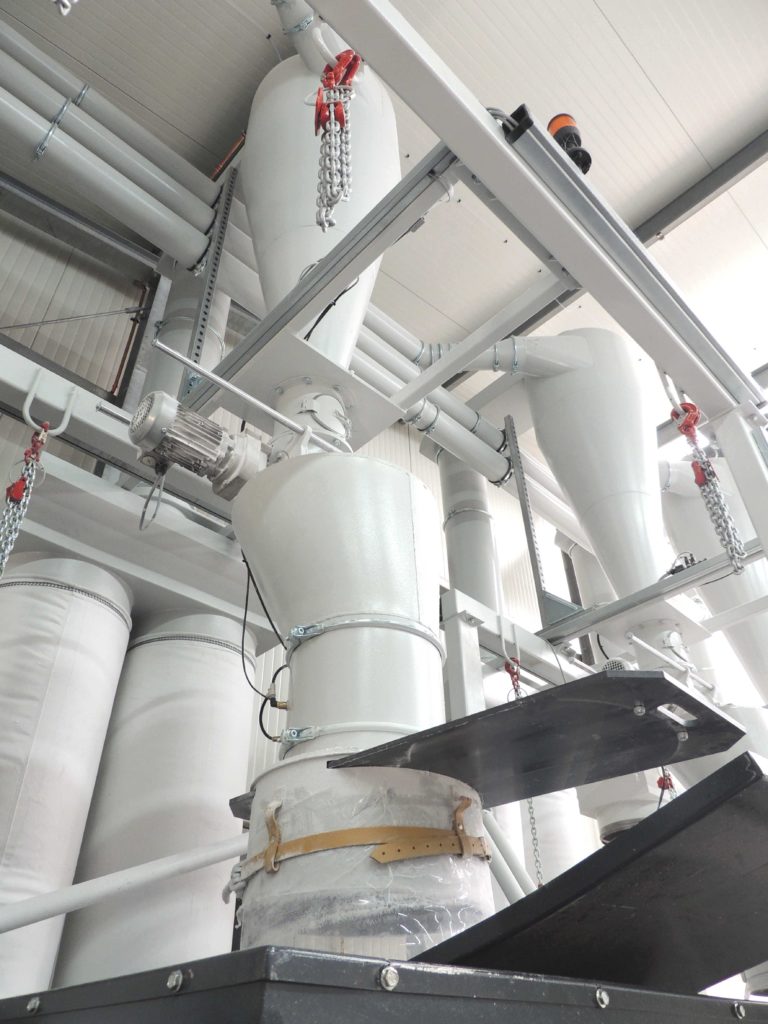
All three new granulation lines as well as another granulator adapted by Getecha Engineering from the Pro-Pac stock are connected to a suction-pressure conveyor system (Getecha System GA 1000) with ground material and exhaust air dust removal. The exhaust air is separated via a cyclone and only released into the surroundings after cleaning by means of exhaust air filters. The ground material from the cyclone ends up – regulated via a rotary feeder – in customer containers, whose filling level is monitored by ultrasound sensors. Once a container is full, an optical signal is issued and the conveyor belt of the respective RS 45090 or the infeed system of the RS 3012 E regulate down, until the container has been replaced. “For the ground material collection containers always being assigned to the correct granulation line, their filling stations are located directly opposite the respective feed in or unwinding station. Full ground material containers are collected as needed and moved back to production. This completes the cycle”, says Plant Manager Kurt Wördemann.
The realisation of the three granulation lines for Pro-Pac is a prime example for the extensive range of services from Getecha. It not only includes the customer-oriented modification and configuration of all rotary cutter granulators (rotors, drive technology, wear protection etc.), but also covers the realisation of the conveyor and material flow systems, the exhaust and de-dusting technology as well as the packaging systems (e.g. Big Bag systems) – the required control technology is always included. “We no longer see ourselves as mere manufacturer of granulators, but also as process-oriented special machine builder with comprehensive engineering and development qualities”, Andreas Lanz states.
Press release October 2018
Plastics technology / extrusion technology / thermoforming / granulation technology / packaging technology / material flow