With its FS 200 and FS 300 foil cutters, Getecha offers manufacturers and operators of film processing plants two high-performance units for the efficient cutting of continuous strips from edge trimming. The compact units can be integrated into the blower or exhaust air flow and can also be combined with the hopper granulators of the rotary cutter family. As a process stage in material preparation, they are used both for processing plastic and aluminium foils and in paper, nonwoven and veneer technology.
Wherever large quantities of endless strips from edge trimming are produced or processed during the manufacture or processing of films, the question arises as to their reconditioning, recycling and return to production. One of the first and indispensable process stages of this cycle is the fast and reliable shredding of the endless strips. To ensure that this is as synchronous as possible with the extraction of the film residues from the production plant, the shredding specialist Getecha has developed the FS 200 and FS 300 foil cutters.
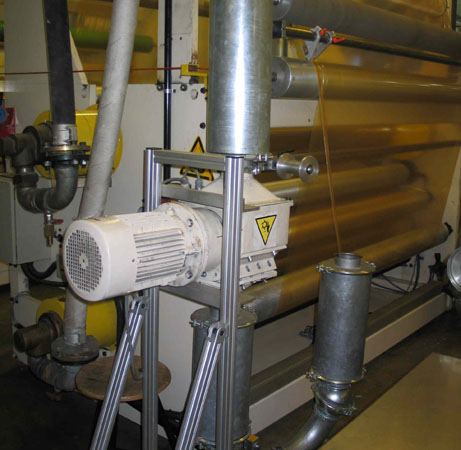
They can be very easily integrated into the piping of the extraction or blower systems and take up almost any kind of edge trim. This means that they can cut foil strips of plastic and aluminium just as effectively as, for example, paper, non-woven and veneer residues. In addition, the Getecha foil cutters are also used in metal cutting applications. Here, they transform the long endless chips from lathes and automatic lathes into short chip strips to reduce the bulk volume and dissolve the tangled material for easier handling.
The Getecha film cutters – here in the picture an FS 200 – are designed so that they can be installed stress-free with two compensators directly into the pipeline of an extraction system.
Close relatives with two or four blades
The FS 200 and FS 300 are designed to be installed stress-free with two compensators directly into the pipeline of an extraction system. In terms of design, the two film cutter models are close relatives, although they differ from each other in important points. Their common features include a robust cast-iron housing and a powerful cutting unit, in which a steel rotor with two regrindable rotor blades and an adjustable, regrindable stator blade operates as standard. As the shaft of the two-blade rotor is not continuous, the rotor offers little resistance to the exhaust air flow and the maximum possible amount of air can pass through the film cutter. For applications with higher throughput rates, Getecha also offers a four-blade rotor as an option, but the continuous shaft of the four-blade rotor then offers greater air resistance.
The differences between the two film cutters become relevant as soon as the concrete application becomes apparent. The Getecha FS 200 is designed for an hourly air flow of 4,000 m3 and has an inlet opening of 205 x 160 mm. The diameter of the rotor or cutting circle is 200 mm. The decisive factor here is that the cutting gap can be adjusted to just 0.02 to 0.03 mm, which allows extremely thin strips of film or paper to be shredded. In order to achieve this narrow cutting gap, the use of high-precision bearings and a torsionally rigid housing is necessary. The rotor is driven by a 2.2 kW electric motor.
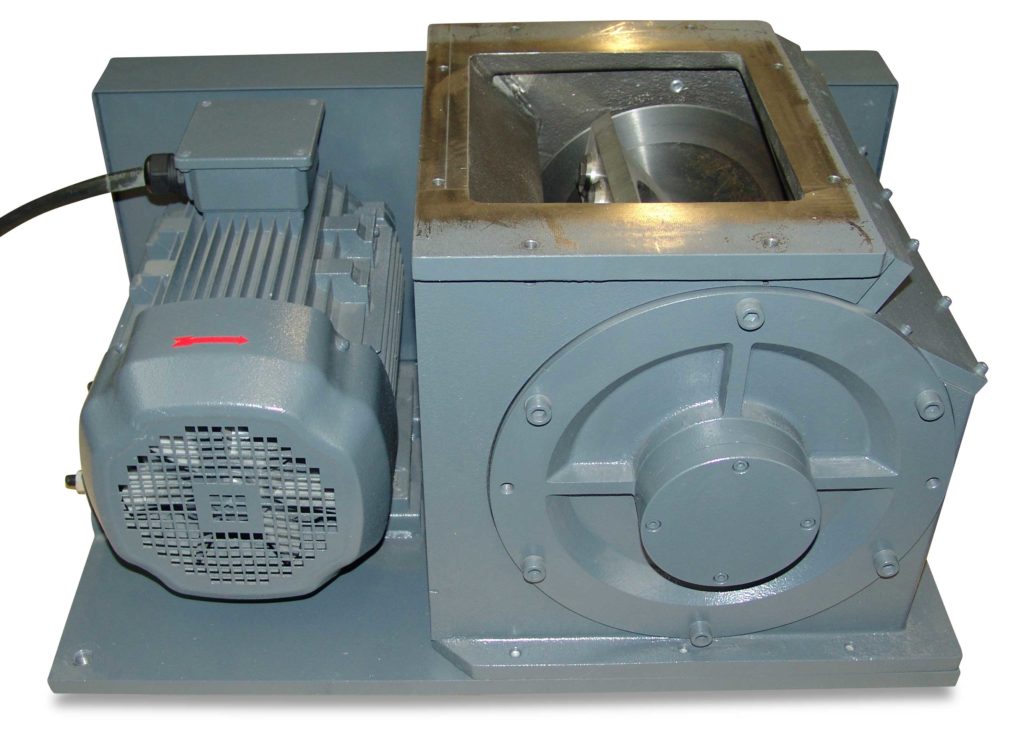
The somewhat larger FS 300, on the other hand, has an inlet opening of 256 x 230 mm, a drive power of 3.0 kW and a rotor diameter or cutting circle of 300 mm. This film cutter is mostly used for coarser applications with higher air flow rates of up to 6.000 m³.
Solo or as system solution
Occasionally, the FS 200/300 is also used by users and plant operators who need to retrofit their extraction systems with additional foil cutters. Very often, however, the Aschaffenburg-based company builds complete granulating lines itself, in which the foil cutters are then combined with the granulators from its own rotary cutter range. In these cases Getecha has the entire project planning and implementation of the plant in its hands – including the control technology and, if desired, the packaging.
Such a granulation line can then look like this in practice: The suction air is generated by a fan above a sealed granulator and flows – together with the endless strip – first through the upstream foil cutter(s). The plastic, aluminium or paper strips can be brought together from different sources via several extraction nozzles and pre-shredded in one or two FS 200/300. The suction air stream then conveys both the pre-cut parts into the granulator for fine comminution and then the ground material into a cyclone separator. If the blower is positioned behind the cyclone, a rotary valve is additionally installed at the material outlet of the cyclone – this is recommended for all wear-intensive applications.
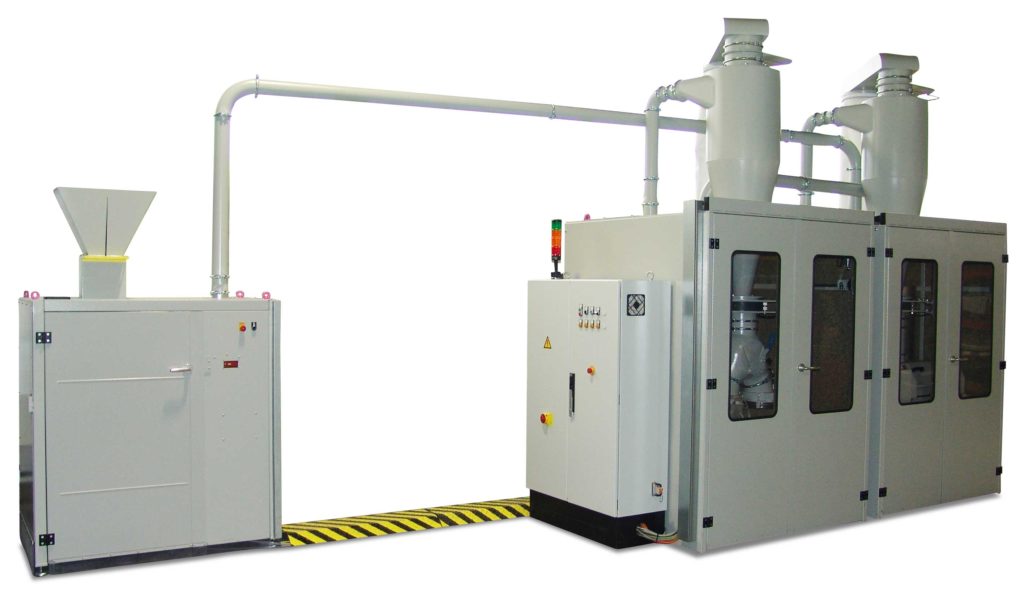
In principle, Getecha’s FS 200 and FS 300 foil cutters can always be used as soloists in the pre-cutting function of foil strip shredding or in combination with a downstream granulator, which then takes over the fine and secondary shredding. Even in technically sensitive areas such as the shredding of security foils for the production of banknotes and credit cards, many plant manufacturers – among others – rely on the foil cutters from Aschaffenburg.
Press release March 2020
Plastics technology / film technology / granulation technology / safety granulation