In an injection moulding production cell, components are inserted into a rotary table by an operator. The parts are checked for manufacturing defects and correct type by an optical inspection system. A handling system puts the checked parts into the injection moulding tool for overmoulding.
The finished parts are put back into the fixtures and are electrically tested. If successful, the parts are finally marked with a laser marking system with a unique code for traceability.
Features:
- modular set-up onto a solid, welded base frame
- rotary table with 8 stations for optical and mechanical inspection of presence, completeness, limits, electric resistivity, electric frequency response and wave form
- marker station for labelling of the finished parts
- standard interfaces for the integration of the customer’s IT-systems
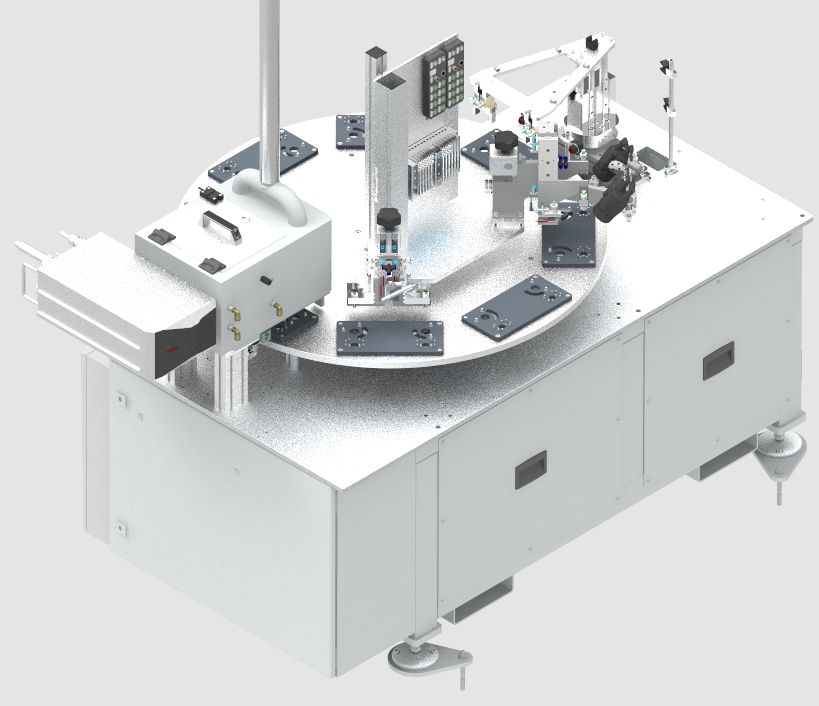